Contact us
Call us at
Available 6:00 AM – 5:00 PM (PST) Business Days
Download
Download Manuals, Datasheets, Software and more:
Feedback

Automotive
Ethernet
Today’s vehicles are generating and transmitting vast amounts of data in order to implement advanced driver assistance systems (ADAS), on-board diagnostics, cameras and sensors, in-vehicle-infotainment systems, and smart safety systems. These in-vehicle networks require much faster speeds than the what has historically been possible using bus like CAN/CAN-FD, LIN, FlexRay, SENT, PSI5, and CXPI networks.
Furthermore, requirements for greater integration between vehicle subsystems are driving fundamental architectural changes with an emphasis on scalable architectures and complex topologies, including gateways connected to a backbone.
Beyond the technical requirements, these in-vehicle networks also need to be lightweight, cost-efficient, and operate in rugged conditions and wide temperature ranges. They also need to be extremely reliable, especially for systems designed to protect the safety of the passengers.
And automotive Ethernet answers all of these demands.
What is Automotive Ethernet?
Automotive Ethernet is a high-speed, low-latency network physical layer. Automotive Ethernet is based on established Ethernet standards, adapted for use in vehicles. It uses a single pair of unshielded twisted wires for light weight and low cost. It is designed to enable the transfer of high volumes of data between in-vehicle modules to support modern powertrain, ADAS, infotainment and comfort systems. There are several different Automotive Ethernet standards, including 100BASE-T1, 1000BASE-T1, and multi-gig automotive ethernet 10GBASE-T1, which can transfer data at speeds from 100 Mb/s to 10 Gb/s.
Benefits of Automotive Ethernet
In vehicles, automotive ethernet components offer many benefits, including:
- High data rates enables high-speed, high-volume data communications
- Low latency provides minimal delay for real-time systems like ADAS
- High reliability with good noise immunity
- Lightweight, space-efficient and cost-effective cabling
- Based on well-established standards from reputable standards bodies
In addition, automotive ethernet is a proven technology that serves the needs for both capacity and integration. Unlike in non-automotive Ethernet, the cables for automotive ethernet use PAM3/PAM4 modulation to achieve high data rates and reliability. While CAN, CAN-FD, LIN and other networks may continue to be relevant in the near future, automotive Ethernet can transport data roughly 100 times faster than a CAN bus and is better suited to meeting the needs of future automotive networks.
Automotive Ethernet Standards
As new applications for automotive Ethernet emerge and speeds become faster, standards organizations release new test and compliance requirements that automotive manufacturers and their suppliers must meet.
The Institute of Electrical and Electronics Engineers (IEEE) has introduced IP-based automotive Ethernet 100BASE-T1 (P802.3bw), Multi-Gigabit Ethernet (IEEE 802.3ch), 1000BASE-T1 (802.3bp) and 10BASE-T1S (IEEE 802.3cg) standards. Most recently, the IEEE introduced the Multi-Gigabit Ethernet (IEEE 802.3ch) standard, which can operate at 2.5Gbps, 5Gbps and 10Gbps with PAM4 encoding scheme.
To ensure the interoperability of hardware and the safe, predictable operation of the vehicle in diverse environments and operating conditions, strict constraints are placed on signal levels, noise, and clock characteristics. The testing techniques specified by the standards, although well-established for stationary Ethernet networks, have created new design challenges for many automotive engineers accustomed to working with slower serial buses like CAN and LIN.
Tektronix can offer vast experience in supporting high speed serial design implementation and troubleshooting, with a variety of instruments and solutions to help engineers test and validate their design, and ensure it is standard compliant.
Validating your automotive Ethernet design
Once a prototype device is built up, it’s time to test its integration with the system and characterize it to make sure it’s within specification.
Tektronix oscilloscopes are an invaluable tool for bringing up and characterizing your automotive Ethernet design.
- Complete characterization under different use cases with advanced measurements and analysis tools
- Automated measurements such as amplitude and time measurements, along with statistical analysis and histograms, are a good place to start to check signal quality
- Eye diagrams are the fastest way to evaluate PAM3 signaling for noise and signal integrity issues
- Jitter analysis tools provide complete profiles of master/slave clock jitter including Time Interval Error (TIE), and cycle-to-cycle, Rj/Dj measurements and isolate the potential source of errors
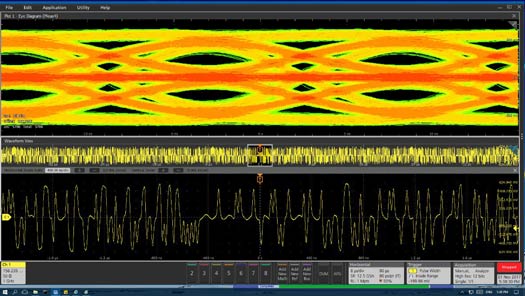
Eye diagrams are the best way to view complex PAM3 waveforms
Speed debugging and troubleshooting your automotive Ethernet design
It’s to be expected that in complex networks systems or components sometimes fail, requiring speedy debug to root cause. Automotive Ethernet’s higher data rates and embedded clocking are sensitive to noise and power variations.
Engineers, used to evaluating waveforms as part of their troubleshooting procedure, often find the PAM3 signals more difficult to debug. Also, since automotive Ethernet is a bi-directional bus it can be more challenging to capture the exact signal of interest.
Tektronix oscilloscopes configured with advanced analysis software provide the tools required for quick and effective troubleshooting if you miss the mark on a spec.
- TIE and histograms to troubleshoot clock recovery problems
- Eye diagrams to quickly evaluate PAM3 signals
- Advanced jitter analysis to identify noise sources by determining whether the jitter is random or deterministic
- Extended triggering functionality
- FFT analysis to isolate sources of interference
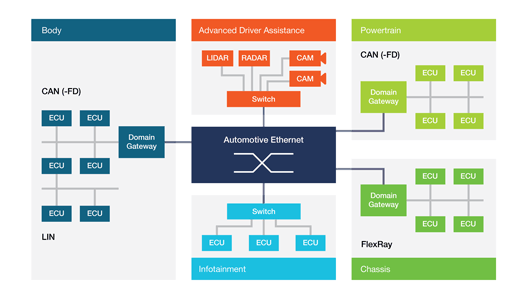
Troubleshooting complex systems requires multi-channel measurements and capable signal integrity tools such as FFTs and jitter analysis.
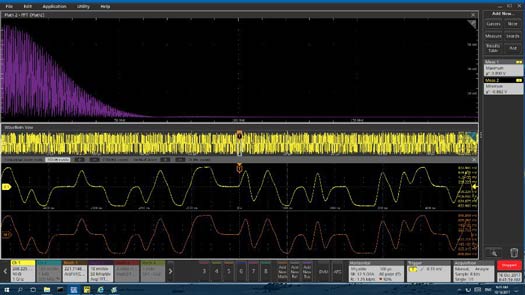
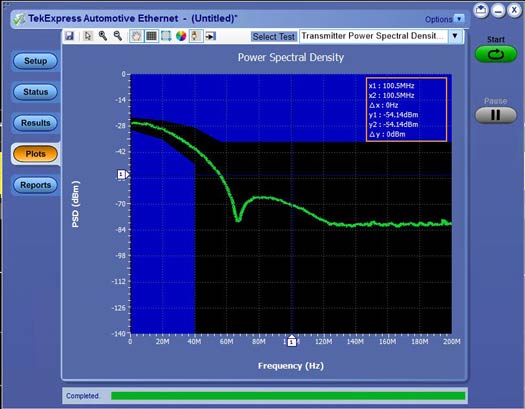
Automated tests such as this Power Spectral Density test, confirm compliance with the standard by comparing results to test limits.
Feel confident your designs are compliant
With greater integration of subsystems into networked environments engineers have to provide verifiable, objective evidence that every device is interoperable; that an individual Electronic Control Unit (or ECU) will reliably communicate with any other ECU. Requirements also extend to ESD and EMC/EMI testing.
However, the adoption of more complex, high-speed Mbps and Gbps serial technologies can be more challenging to test.
Tektronix has been involved in high-speed compliance testing for many years and is applying this expertise to testing newer technologies in automotive. Compliance solutions include support for 100BASE-T1 (802.3bpTM) and as well as BroadR-Reach or 100BASE-T1 (802.3bwTM). The latest compliance solution is for Multi-Gigabit Ethernet (IEEE 802.3ch) and 10BASE-T1S (802.3cg). All adhere to the testing requirements defined by the OPEN Alliance. Tektronix oscilloscopes and spectrum/signal analyzers can also be applied for ESD and EMC testing.
Introducing signal separation for automotive Ethernet testing
Signal characterization and protocol testing can create challenges from design to validation to maintenance. Seeing actual data between ECU#1 and ECU#2, assessing signal integrity in Full Duplex mode and examining Protocol data at the system level without breaking the automotive Ethernet cable add test complications, time and expense. Tektronix’ unique, patent pending, Signal Separation solution overcomes the shortcomings of current offerings in the market, enabling customers to:
- Separate traffic from ECU#1 and ECU#2 in Full-Duplex mode without having to cut cables or make hardware changes to the automotive Ethernet cable
- Simultaneously display ECU#1 and ECU#2 Protocol decode data
- Perform Protocol decode in Full-duplex mode
- Automotive Ethernet PAM3 and Signal Separation Introduction
- Automotive Ethernet: See the True Signal
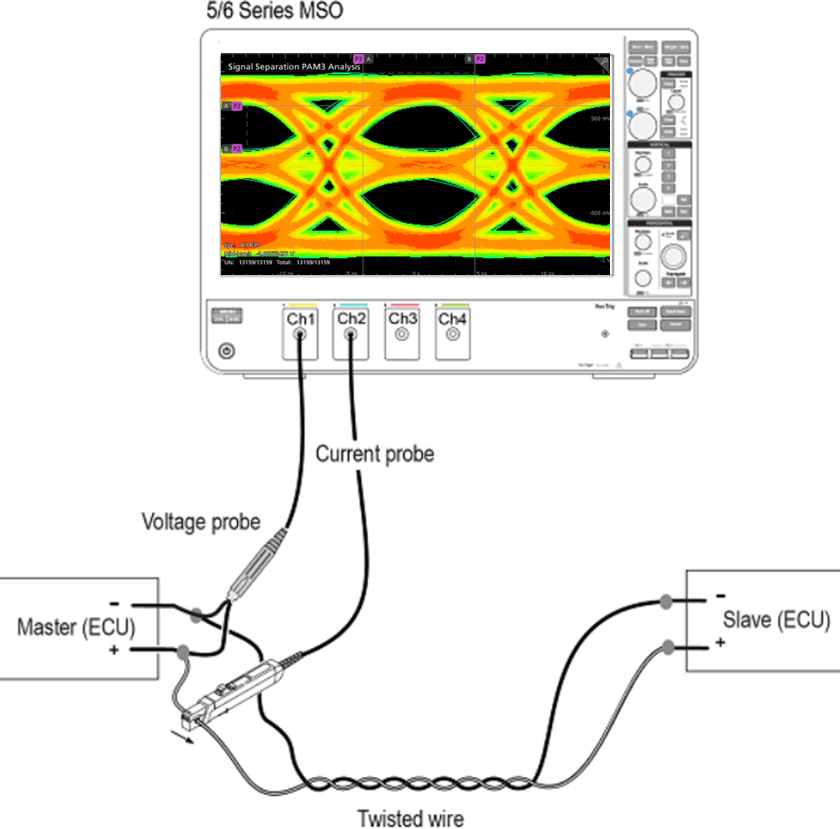
Automotive Ethernet testing solutions
Testing an automotive Ethernet design often requires an automotive oscilloscope, appropriate probes, a signal source, software and appropriate test fixtures. To meet your needs, Tektronix offers a full line of test solutions for Signal Quality and Compliance.
Automotive Ethernet Test | Oscilloscope | Software | Probes | Signal Source | Fixture |
---|---|---|---|---|---|
Signal Quality Testing (Signal Separation, Protocol Decode, Signal Quality & Debug) |
![]() ![]() |
Option 5/6 -AUTOEN-SS: Signal Separation Option 5/6 -PAM3 (Automotive Ethernet Signal Analysis) Option 5/6 -SRAUTOEN1 (100BASE-T1 Protocol decode) Opt. 5/6 -DJA (Jitter Analysis) |
|
ECU Dependent Contact Tektronix for information |
|
Open Alliance/IEEE PMA Tx Compliance test |
![]() ![]() |
Opt. 5/6-CMAUTOEN10 (10BASE-T1S compliance) |
|
AFG31000 series (Return loss) | TF-XGBT |
Opt. 5/6-CMAUTOEN (100BASE-T1/1000BASE-T1 compliance) |
|
AFG31000 or AWG5200 series (Distortion and Return loss) | TF-XGBT, TF-BRR-CFD | ||
![]() |
Opt. BRR (100BASE-T1/1000BASE-T1 Compliance) |
|
AFG31000 or AWG5200 series (Distortion and Return loss) | TF-XGBT, TF-BRR-CFD | |
![]() ![]() |
Opt. AUTOEN10G (Multigigabit Ethernet Compliance) |
|
NA | PCB S3401 SB 396373*1 |
Automated testing software may be installed on a new instrument, added to an existing instrument, or shared among a fleet of scopes in the same series. Contact Tektronix for more information.
Automotive Ethernet Resources
This application note describes ways to separate full-duplex automotive Ethernet communication.
An overview of the trends, challenges and solutions associated with in-vehicle networks, especially validation and conformance testing.
This webinar offers insights into the new measurement requirements for the latest automotive multigigabit Ethernet (10Gbps) compliance testing.
See how Tek’s automated application can help with automotive multigigabit Ethernet (IEEE802.3ch) compliance testing.
Volkswagen plans to reduce the number of ECUs in cars from 70 to three. In this blog, the Tek team discusses how this will impact testing for automotive manufacturers and suppliers.
Automotive Ethernet test instruments
5 Series MSO Mixed Signal Oscilloscope
- Automotive Ethernet compliance test package automates testing per industry standards
- Integrated eye diagrams and optional jitter analysis help validate signal integrity
- 350 MHz to 2 GHz
- Up to 8 input channels
- 15.6” high definition pinch/swipe/zoom touchscreen provides more analysis area
6 Series B MSO Mixed Signal Oscilloscope
- Automotive Ethernet compliance test package automates testing per industry standards
- Integrated eye diagrams and optional jitter analysis help validate signal integrity
- Exceptional noise performance, especially at high sensitivity
- 15.6” high definition pinch/swipe/zoom touchscreen
DPO70000SX ATI Performance Oscilloscope
- DPO70000SX ATI Performance Oscilloscopes deliver the industry’s most accurate capture of high-speed signal behavior to verify, validate, and characterize your next generation designs.
- Broad range of standards support, including MIPI, DisplayPort, HDMI, PCIe Gen3/Gen4/Gen5, SATA/SAS, USB3.1, Type-C, and 10/100BaseT to 10G/100G Ethernet
Facing challenges in other connected car applications?
Automotive Ethernet FAQs
Why is Ethernet used in automotive?
Because today’s vehicles are transmitting more data than ever before, they require faster speeds, greater integrations between subsystems, and more complex topologies than in the past. Ethernet meets these technical requirements while remaining cost-efficient and lightweight, and it can endure the rugged conditions vehicles operate under.
What is the future of automotive networks?
With on-board diagnostics, cameras, sensors, and advanced driver assistance, infotainment, and smart safety systems, vehicles will continue to require more and more data to be transferred faster and more reliably than ever before. And automotive Ethernet is emerging as the network of choice for cars of the future.
What is automotive Ethernet used for?
Automotive Ethernet is a form of Ethernet network standard that is used to connect sub-systems and components over an unshielded twisted pair (UTP) within an automotive. It is designed to meet the needs of the automotive market, including meeting electrical requirements (including EMI/RFI emissions), bandwidth requirements, latency requirements, and synchronization requirements.
What is the speed of automotive Ethernet?
10Base-T1S is a 10Mb/s Automotive Ethernet described in the IEEE802.cg standard.
100Base-T1 is a 100Mb/s Ethernet standard described in IEEE802.3bw standard.
1000Base-T1 is 1Gb/s Automotive Ethernet described in IEEE802.3bp. IEEE 802.3ch for three data rates: 2.5GBase-T1 at 2.5Gb/s, 5GBase-T1 at 5Gb/s, and 10GBase-T1 at 10Gb/s.
In future, IEEE 802.3cy, 25 and 50 Gb/s