Contact us
Call us at
Available 6:00 AM – 5:00 PM (PST) Business Days
Download
Download Manuals, Datasheets, Software and more:
Feedback
Reliable Precision with Tektronix Calibration Services
As a dedicated Lab Manager or Maintenance Coordinator, you know the importance of precision and reliability. Tektronix calibration services are designed to help you achieve exceptional accuracy and efficiency in your operations.
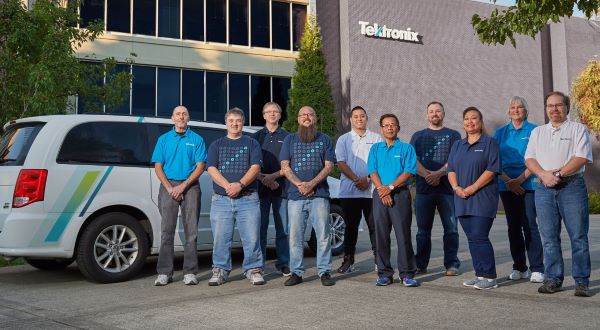
Calibration Services Options
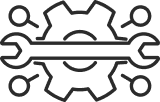
Tektronix & Keithley Factory Verified Calibration Services
Factory-grade calibration services for your Tektronix and Keithley instruments.
Comprehensive Maintenance Checks: Includes preventative maintenance across the full range of instrument operation.
Firmware and Software Upgrades: Update to the latest features and enhancements with each calibration.
Out of Tolerance Adjustments: Provides instrument adjustment for out of tolerance calibration.

Multi-Brand OEM Compliant Calibration Services
Mixed brands on your bench? Tektronix calibrates over 140,000 products from 9,000+ manufacturers.
OEM Specification Compliance: Calibration follows the exact points and procedures recommended by the instrument OEM.
Simplify Calibration for Your Instrument Fleet: A single service partner for all your calibration needs.
Tailored Calibration Service Delivery Options: Choose from In-Lab, Periodic Onsite, Permanent Onsite, Virtual Onsite, or Mobile Lab calibration services.
Compare Calibration Services
Tektronix & Keithley Factory Service Calibration | Multi-Brand OEM Compliant Calibration Services | |
---|---|---|
Equipment Serviced | ||
Tektronix & Keithley Equipment |
|
|
Over 140,000 products from 9,000 manufacturers |
|
|
Services Performed | ||
Calibration as recommended by manufacturer |
|
|
Out of Tolerance Instrument Adjustments |
|
|
Checks for full range of instrument operation |
|
|
Software and firmware upgrades |
|
|
Exhaustive Cleaning Process |
|
|
Service Levels | ||
Standard Calibration |
|
|
Standard Calibration with Data |
|
|
Accredited Calibration |
|
|
Service Delivery Options | ||
In Lab |
|
|
Periodic onsite |
|
|
Permanent onsite |
|
|
Virtual onsite |
|
|
Mobile onsite |
|
Expert Calibration Services Suited to Your Needs
What is the difference between Factory-Verified & OEM Compliant Calibration?
In the precision-driven world of calibration, understanding the nuances between different types of services is crucial for ensuring your instruments perform optimally. Tektronix, a leader in calibration technology, offers two distinct calibration services: Factory-Verified Calibration and OEM Compliant Calibration.
Why Do I Need an Accredited Calibration?
Precision is essential for reliability and quality in electronic test and measurement. Accredited calibration ensures accurate measurements, which is crucial for lab managers, calibration coordinators, and industries relying on measurement accuracy.
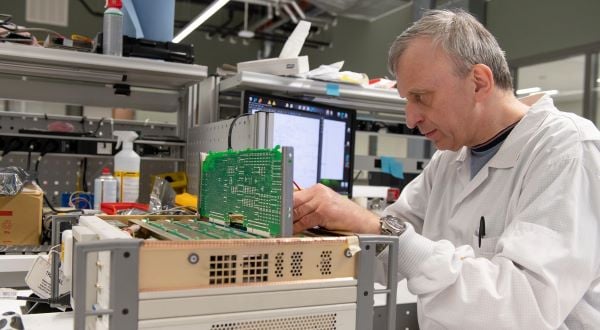
High-Quality, Accurate & Accredited Calibration Service
Our skilled Calibration Technicians and Customer Service Engineers ensure your test equipment undergoes meticulous calibration, following rigorous certification and NIST traceability standards. With Tektronix, trust that your instruments are in expert hands for consistent precision and reliability.
Tailored Solutions for Your Specific Needs
Every operation has its own set of needs and challenges. Our team collaborates with you to understand your goals and develop customized calibration solutions that boost innovation and production efficiency.
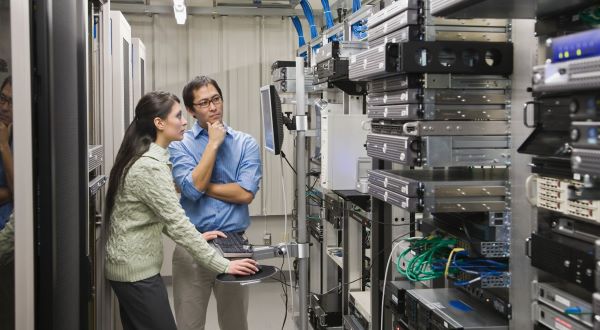
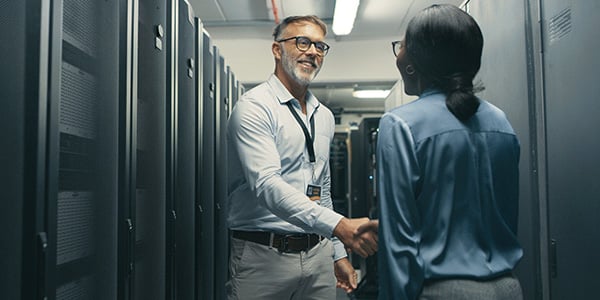
Trusted Partnership Approach
At Tektronix, we’re more than service providers; we’re partners in your success. Our focus on long-term relationships ensures you receive superior service, ongoing support, and collaboration to achieve your operational goals.
Global Calibration Service Locations
Time is of the essence, and we recognize the importance of having access to fast and convenient service. With our strategically located service centers, you can benefit from prompt support whenever and wherever you need it.
Calibration White Papers and Case Studies

Lean Calibration Process Case Study
Discover how Tektronix's quality calibrations have helped a large aerospace company improve efficiency, reduce costs, and maintain exceptional on-time calibrations for their sophisticated test and measurement equipment, ensuring a smooth production flow and continuous improvement.

Turnaround Time Savings Case Study
Uncover how Tektronix's calibration services helped a large semiconductor company achieve an impressive 82% reduction in calibration turnaround time, boosting productivity and equipment availability.
Testimonials - Calibration Services
On-Demand Calibration Webinar
Quality calibration is the key to confidence in your measurements. Our calibration experts, Jack Wojewski and Guy Robinson, will discuss several factors to consider to ensure the quality of the service you are getting. We'll answer the following questions:
- Why is calibration important?
- What is a quality calibration?
- What should you look for in a calibration provider?
- What should you include in a request for calibration?
- How do you read scope of accreditation documents?
Frequently Asked Questions - Calibration Services
What is calibration?
Calibration is the comparison of a measurement device (an unknown) against an equal or better standard. Calibration is all about confidence in the measurement results you're getting and assures you that your measurements are accurate within the specification limits that led you to select the instrument in the first place.
A "typical" commercial calibration references a manufacturer's calibration procedure and is performed with a reference standard at least four times more accurate than the instrument under test. The risks of not calibrating include false passes or false failures in production resulting in costly reworks or discarding products. Traceable calibrations also ensure adherence to the international standards that our commerce relies on.
Even though today's digital instruments are inherently are more stable than their analog predecessors, their tolerances are much narrower than in the past. And even the latest digitizing instruments have analog circuitry—preamplifiers, buffers, etc.—whose performance can change over time. A regular schedule of calibrations will keep your instruments in optimal condition to support your design, troubleshooting, and manufacturing work.
Why should I calibrate my instrument?
Calibration ensures measurement accuracy. Routine calibrations are your prescription for the continued health and performance of your instrument. There are also costs and risks associated with not calibrating equipment regularly.
Calibration should be part of your engineering process. It validates your measurements over a period of time and reduces the risk of rework, recalls, returns and repairs. With proper calibration you can be more efficient with your time to market and reduce your total cost of test. In the engineering lab, inaccurate measurements can distort your findings about the behavior of an emerging design. You don't want to go through unnecessary design rework because your instrument was inaccurate during design validation.
There also may be regulatory requirements stipulating a regular calibration schedule. Penalties for non-compliance from an audit may be fines, loss of business, plant shut down or worse.
Some of our equipment is difficult to move. How do we get it calibrated?
Sometimes sending in an instrument to get calibrated isn't an option. From onsite service to local service centers, there are different delivery options available to meet your needs.
Local service centers – Local service centers offer free pick-up and delivery within the locality of the center, and a broad scope of accreditation which helps minimize third-party costs.Tektronix has 27 North American and 18 International locations. Find a service center nearest you.
Periodic onsite service – With this option, customers can plan ahead and avoid having to take equipment out of service to minimize impact on your design and production schedules. This is also the best option to calibrate sensitive or large equipment that can’t be moved.
“Virtual onsite service” – With the concerns surrounding the ongoing COVID-19 pandemic, we’ve also introduced a new “virtual onsite” service where we dedicate the resources and standards that would have been used for onsite service but perform the service in our service center. Virtual onsites, combined with pickup and delivery service, allow for appropriate social distancing where required and offers the same fast turnaround times you would experience with a normal onsite service event.
What is a calibration certificate?
A calibration certificate is an essential and official document that serves as a record for the calibration of instruments, offering a critical aspect of traceability to the National Institute of Standards and Technology (NIST). The integrity and accuracy of this certificate are indicative of the credibility and validity of the organization conducting the calibration. A Calibration Certificate accompanies the instrument when it's returned to its owner, documenting crucial information about the instrument's condition, including out-of-tolerance conditions and special measurement circumstances.
Calibration certificates may vary in format due to geographical and regulatory differences, but they typically include details such as calibration dates, environmental conditions, in-tolerance or out-of-tolerance conditions, traceability statements, and information about the calibration procedure and intervals. Understanding and preserving this certificate is vital for assessing measurement accuracy and mitigating risk associated with uncertainties in measurements.
What is your calibration interval?
Determining the right calibration interval for your test and measurement equipment depends on many factors with no “one size fits all” approach available.
Learn what factors can influence your test equipment’s measurement accuracy and what to consider when determining your calibration interval.
What is metrology?
Metrology ensures that your calibrated instruments deliver accurate results with provable validity. The mission of metrology is to maintain measurement standards, to develop effective new methods, and to ensure that measurements are accepted uniformly around the world.
Why calibrate? Your instruments need to be calibrated against known standards so their results can be trusted to have a universally accepted meaning. Metrology is the science that supports this trust—in both the "meaning" and the measurements:
- Metrology defines calibration and ensures predictable performance from your measurement tools.
- Metrology is the discipline that defines standards and codifies accreditation and traceability.
- Metrology expertise is at the heart of Tektronix' reputation for accuracy, precision, and performance.
At Tektronix, metrology professionals guide calibration policies and procedures at accredited calibration facilities around the world. When you choose Tektronix as your service provider, you get the benefit of an experienced metrology staff plus seasoned technicians applying deep product-specific knowledge.
The result? Services guaranteed to be of the highest quality in the industry.
What is the difference between calibration and validation?
Calibration is the comparison of a measurement device (an unknown) against an equal or better standard, and validation involves documenting that a system or process provides an expected and consistent outcome.
Calibration Terminology
Demystify the calibration process with a better understanding of these key terms.
Helpful Calibration Links
- Asia-Pacific Metrology Program (APMP)
- Bureau International des Poids et Mesures (BIPM)
- Euro-Asian Cooperation of National Metrological Institutes (COOMET)
- European Collaboration on Measurement Standards (EUROMET)
- European Co-operation for Accreditation
- European Cooperation in Legal Metrology (WELMEC)
- Inter-American Metrology System (SIM)
- International Earth Rotation Service
- International Electrotechnical Commission (IEC)
- International Journal of Metrology and Quality Engineering
- International Lab Accreditation Cooperation (ILAC)
- International Organization of Legal Metrology (OIML)
- International Society for Weighing Measure
- International Society for Optics and Photonics (SPIE)
- International Standards Organization
- NCSL International (National Conference of Standards Laboratories)
- Pacific Accreditation Cooperation
- South African Development Community Cooperation in Measurement Traceability