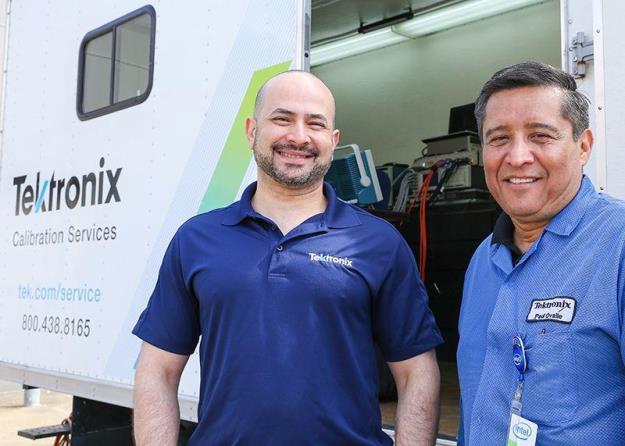
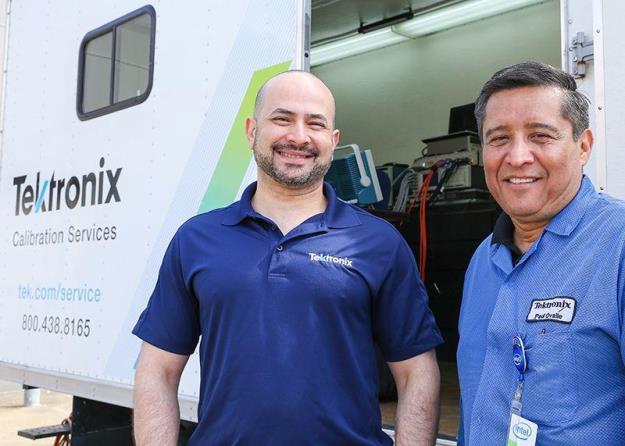
Keeping your test and measurement instruments in compliance and in service is vital to maintaining efficient R&D and production operations. Going line-down because of equipment calibration is aggravating at best, and detrimental to your bottom line at worst. Lab managers, quality managers, and calibration coordinators are constantly looking for ways to streamline their calibration programs and limit disruption to production.
Some of the larger labs in mission-critical industries are increasingly turning to onsite calibration services to satisfy their program’s requirements. To decide if onsite calibration is right for you, here are some questions to ask yourself:
- What is your tolerance for de-racking?
The most basic consideration when evaluating onsite calibration services is convenience. When you have a lab full of equipment, hiring a provider to come onsite and calibrate everything that is due at once is a huge time saver. No more time spent taking equipment out of rack and stack systems, shipping it to a provider, and then rebuilding your racks when the equipment is shipped back to you.
- How movable is your electronic test & measurement equipment?
Some equipment must be calibrated onsite. Large or sensitive instruments can be risky to move and are better be calibrated in place. Why not calibrate the rest of your equipment while your service provider is onsite?Calibrating your electronic test and measurement equipment onsite also enables you to avoid several potential risks associated with shipping equipment. Your lab is full of sensitive equipment that could see damage from vibration or electrostatic discharge during the shipping process. Calibrating your sensitive equipment onsite gives you peace of mind and saves you time and money preparing your equipment to be shipped.
- How important is regular, predictable scheduling?
Onsite calibration service calibrates several instruments at once so you can spend less time managing service engagements and enjoy a more predictable calibration schedule. You can set up annual, semi-annual, or more frequent onsite calibration service events depending on your equipment’s calibration status to make sure you are staying in compliance and one step ahead of auditors.
- What is your tolerance for disruption and/or downtime?
Onsite calibration service can significantly minimize disruption to your operations. Calibrating your equipment in place means you don’t have to go without instruments for extended periods of time or invest in redundant equipment just to avoid downtime.
Additionally, calibration turnaround time is dramatically reduced when choosing onsite calibration services. Onsite instrument calibration engagements typically are completed same day or within a few days.
What Should You Look for in an Onsite Calibration Service Provider?
Proven Calibration Quality. First, mission-critical industry customers who need to pass audit should pay attention to the quality and accuracy of the calibration. Consider test and measurement manufacturers like Tektronix, who are uniquely qualified to provide OEM-level calibrations. Check the price differences between manufacturers to ensure you are paying a fair market price for that extra quality and peace of mind. Tektronix, for example, performs onsite calibration services and is certified to perform ISO/IEC 17025 calibrations on a wide variety of equipment.
Official Accreditation. Your calibration service provider should have a broad scope of accreditation, meaning a third-party accrediting body like A2LA has verified the provider has the capabilities and expertise to provide a quality calibration for a wide variety of equipment. Your lab is full of various equipment types from different brands, so finding a single-source provider that is qualified to calibrate a wide breadth of equipment is vital to performing a successful onsite calibration.
Breadth of Service Levels. Calibration service providers should also be able to provide the exact service level your organization’s quality policy dictates, whether it is a full 17025 accredited calibration or a simple out of tolerance calibration.
Which Onsite Calibration Service Delivery Option is Right for You?
Periodic Onsite Calibration – This is the most common service option where a calibration service provider like Tektronix sends service engineers to your lab with the appropriate lab standards to calibrate a batch of equipment on a regular schedule.
Virtual Onsite Calibration – Like a physical onsite calibration, lab resources are dedicated to calibrating a batch of your equipment. However, instead of calibrating the equipment in your facility, the equipment is carefully packaged and transported to a local service center to be calibrated, where “reserved” technicians are ready to perform the service. This option is used mostly for labs where the presence of outside personnel has been restricted due to COVID-19, security, or other parameters. This option enables organizations to stay compliant with health and safety protocols while taking advantage of the fast turnaround times of an onsite calibration.
Permanent Onsite Calibration – Some calibration service providers, like Tektronix, can embed service engineers permanently at your facility to augment your existing calibration team or to fully manage your calibration program. Having a technician onsite means that you’ll see ultra-fast turnaround times and can quickly respond to emergencies or changing priorities.
Hybrid Approach – Ensure your calibration services provider can put together a custom program that meets your exact needs. At Tektronix, this is where we shine. We’ll work with you to develop the best solution for your business based on your requirements. For example, you may decide that it makes the most sense to calibrate your sensitive electronic test equipment onsite but send your dimensional instruments to a service center to be calibrated.
Onsite Calibration In Practice
Theoretical discussion is great, but how does onsite calibration actually work?
Tektronix had a permanent onsite technician, Keith, embedded at Sandia National Labs for 30 years. Keith serviced various types of equipment in support of Sandia’s particle accelerator beam program including Tektronix digitizers and data recorders. Keith maintained a 1-3 day turnaround time for equipment calibration and has been instrumental in helping Sandia adapt to changing circumstances, maintain compliance, and limit downtime. Keith recently retired with a job well done.
Jerry Mills, Senior Information Systems Architect at Sandia notes, "Keith and Tektronix help us pull a recorder from our system, get a calibration or repair performed, and place it back into the system within a day or two. Sometimes even within hours. This capability has allowed us to operate our multichannel recording system without needing additional, expensive recording assets to be 'on-the-shelf’ as spares and has allowed us to use practically 100% of our digitizer resources to record waveform data."
Conclusion
Onsite calibration is a smart option if you want convenient service with the least amount of disruption and risk. You’ll see faster turnaround times and reduced downtime. As your partner, Tektronix works with you to create and deliver the best onsite calibration solution for your unique business requirements. Learn more about our service delivery options and read more about Keith’s work at Sandia.