Contact us
Call us at
Available 6:00 AM – 5:00 PM (PST) Business Days
Download
Download Manuals, Datasheets, Software and more:
Feedback
Understanding EMI and EMC Testing: Conducted and Radiated Emissions
Did you know that 50% of projects fail EMI/EMC testing the first time? Intertek Testing Services reports that roughly half of products fail the initial EMI/EMC tests due to a failure to apply EMC principles, lack of EMI/EMC knowledge, incorrect applications of regulations, unpredicted interactions among circuit elements, or incorporation of non-compliant modules or subassemblies into the final product.
Performing pre-compliance testing greatly improves the probability of a successful first pass of full EMI/EMC compliance testing, saving you time and thousands of dollars. EMI testing, in particular, involves debugging to identify and mitigate sources of electromagnetic interference, ensuring that your product meets regulatory standards. Companies designing products for medical, automotive, military, and even multimedia applications can benefit from investing in a pre-compliance test setup. This page discusses how adding pre-compliance testing to your product development process can accelerate product development and reduce project costs. Learn more about the basics of EMI/EMC testing.
What is EMI/EMC Testing?
Electromagnetic Compatibility (EMC) and Electromagnetic Interference (EMI) testing are crucial processes in ensuring that electronic devices operate correctly in their intended environments without causing or being affected by unwanted electromagnetic disturbances.
EMI Testing measures the electromagnetic emissions from a device to ensure they do not interfere with other electronic equipment. This is important because excessive emissions can disrupt the operation of nearby devices, leading to malfunctions or failures.
EMC Testing evaluates a device’s ability to function properly in the presence of electromagnetic interference. This ensures that the device can operate as intended without being affected by external electromagnetic fields.
A complete EMI/EMC pre-compliance solution
To affordably speed you on your way, Tektronix offers a complete EMI/EMC pre-compliance testing solution including software, spectrum analyzers, accessories and EMC near-field probes.
EMC Software
Tektronix EMI/EMC pre-compliance solution starts with SignalVu-PC with EMCVu software. As a plug-in to SignalVu-PC, EMCVu provides a single user interface for all your pre-compliance needs.
Spectrum Analyzers
To provide fast, accurate measurements to assist you in finding EMI/EMC issues quickly, Tektronix offers a full line of affordable Real-Time Spectrum Analyzers. Real-Time Spectrum analyzers provide significant advantages over traditional swept enabling you to capture infrequent EMI bursts.
EMI/EMC Testing Equipment
Pre-compliance software for ease of use
SignalVu-PC with EMCVu
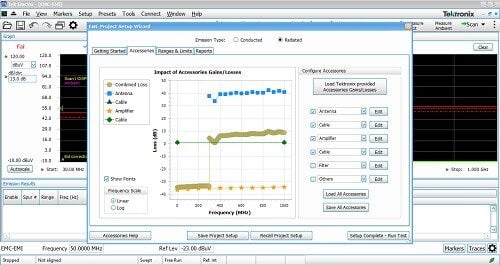
Tektronix EMI/EMC precompliance solution starts with SignalVu-PC with EMCVu software. EMCVu gives you an easy-to-use interface with all your precompliance measurements built-in. Simply purchase the EMCVu software license to unlock its capabilities within SignalVu-PC.
Pre-compliance at a fraction of the cost
Real-Time Spectrum Analyzers
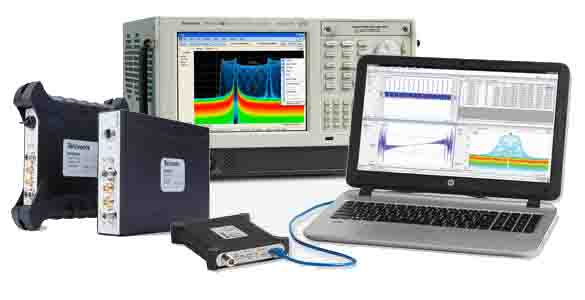
Tektronix Real-Time Spectrum Analyzers help you discover elusive emissions that traditional spectrum analyzers miss. All Tektronix spectrum analyzers include SignalVu software for extensive spectrum analysis
Mixed domain analysis in highly-integrated oscilloscopes
4/5/6 Series MSO Oscilloscopes
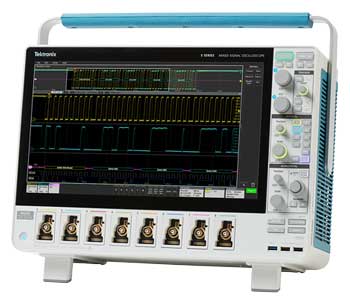
These versatile oscilloscopes offer a distinctive Spectrum View that allows any analog channel to show a time domain waveform, a spectrum, or both. The time and frequency plots are synchronized to help you determine which signals are the victims and which ones are the aggressors.
Synchronized time and frequency analysis
MSO4000 Series

Use powerful trigger, search and analysis tools to zero in on EMI signals and correlated analog, digital and RF anomalies. The MSO4000 Series includes a logic analyzer, spectrum analyzer and protocol analyzer – all synchronized for an integrated view.
Benefits of EMC pre-compliance testing
When you're working to get your new design to market fast, the last thing you want is to get held up by compliance testing failures at the end of your design cycles. Incorporating a precompliance solution into your work processes gives you many benefits:
- Early identification of potential EMI/EMC issues that may delay time-to-market and increase development costs
- Reduction of EMI/EMC related costs
- Increased confidence in your product before you take it to the test house
- Immediate feedback on the impact of design changes
- Flexibility to test on your schedule
Continue learning about pre-compliance EMC testing with our comprehensive guide.
Good EMC design techniques are not too difficult to implement if they are introduced at the earliest stages of design. If modifications need to be made later in the design to meet EMC requirements, it becomes much harder.
Demystifying EMI/EMC test setups
A typical radiated test set-up with a Tektronix RSA500 USB spectrum analyzer.
EMI/EMC pre-compliance testing doesn’t have to be hard or excessively time consuming. Based on customer feedback, Tektronix developed next-generation software with ease of use and functionality in mind, to provide pre-compliance testing for radiated and conducted measurements.
Setting up EMI/EMC pre-compliance testing starts with SignalVu-PC. This latest version of SignalVu-PC now comes with an additional option called EMCVu. EMCVu features an easy-to-use setup wizard, built-in standards and accessory setup with push-button selection capabilities. Whether you are setting up an Open-Air Test Site (OATS), or testing in your lab, EMCVu streamlines the capture and removal of ambient noise from your measurements to increase the accuracy of your pre-compliance tests without an anechoic chamber.
To learn more about using EMCVu with real time spectrum analyzers and accessories to perform pre-compliance tests for radiated and conducted emissions, download the application note here.
If you’re interested in trying a free 30-day trial of EMCVu, please click on the button below.
Standards supported by Tektronix EMI/EMC pre-compliance solutions
Tektronix’ EMCVu pre-compliance software supports EMC standards including CISPR, FCC and MIL-STD for many types of devices. To automate testing, EMCVu provides a built-in standards table allowing you to choose the applicable standard for your product and the region it will be sold in. EMCVu also allows you to configure standards not included with the ability to set frequency ranges or limit line tables for your chosen standard.
A quick summary of supported standards is below:
MARKET SEGMENTS | Equipment Type | STANDARDS | ||||
---|---|---|---|---|---|---|
IEC/CISPR | CENELEC/EN | FCC | MIL-STD | DEF-STAN | ||
ISM MEDICAL | Industrial, scientific and medical equipment | CISPR 11 | EN 55011 | CFR Title 47 Part 18 | ||
Medical electrical apparatus | EN 60601-1-2 | |||||
AUTOMOTIVE | Vehicles, boats and internal combustion engines | CISPR 12 | EN 55012 | CFR Title 47 Part 15(*) | ||
Components and modules on board vehicles | CISPR 25 | EN 55025 | ||||
MULTIMEDIA | Sound and TV broadcast receivers | CISPR 13 | EN 55013 | CFR Title 47 Part 15 | ||
Information technology and telecommunications equipment (ITE) | CISPR 22 (superseded by EN55032) | EN 55022 (superseded by EN55032) | ||||
Professional audio/video/multimedia equipment | CISPR 32 (replaces CISPR 13 and 22) | EN 55032 | ||||
APPLIANCES | Electrical devices, household appliances and tools | CISPR 14-1 | EN 55014-1 | CFR Title 47 Part 15 | ||
LUMINAIRES | Fluorescent lamps and luminaires | CISPR 15 | EN 55015 | CFR Title 47 Part 15 | ||
MILITARY | Military equipment and systems | MIL-STD-461G | DEF-STAN 59-411 |
Troubleshooting tips to speed up debug work
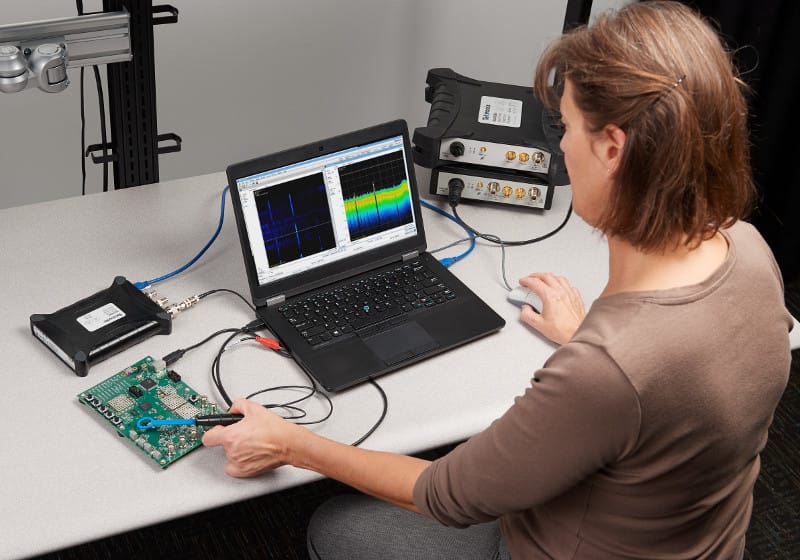
Before you invest the time and money in final product certification testing, you want confidence that your device is ready to go to the test house. When you run into a problem, you want the right tools that allow you to focus on problem areas quickly, identify the cause and take steps to remediate without incurring costly delays.
To efficiently debug, look for a solution that lets you quickly identify areas of concern and provides the level of signal insight that captures intermittent offenders. This is delivered by a combination of hardware and software.
Some of capabilities you should look for in your software solution include:
- Quasi-Peak detector which lets you bypass non-failures and zero in on frequencies of interest.
- Harmonic Check which allows you to test only specific harmonics and find where those emissions come from on a board using a near field probe.
- Harmonic Markers which enables finding emissions at harmonics of a known frequency.
- Multiple Traces allowing you to compare the Device Under Test (DUT) to Ambient Noise, previous iterations of a Device, etc.
- Automated or manual multi-failure re-measurement, allowing you to determine if a failure is intermittent or reoccurring.
- Report multiple measurements in multiple formats in the same user configurable report.
With hardware, Real-Time Spectrum Analyzers make EMI debug much easier. Some of the benefits provided by a real-time spectrum analyzer include:
- The ability to capture transient and intermittent signals.
- The ability to debug multiple sources at the same frequency.
- Instantaneous feedback – traditional swept spectrum analyzers sweeps can take longer and result in failure in capturing important signals.
To learn more on how to use our Real-Time Spectrum Analyzers for emissions pre-compliance testing on our blog here. Additional information on troubleshooting techniques are available in the “Practical EMI Troubleshooting” application note that you can download by clicking on the button below.
Download AppnoteTroubleshooting EMI with mixed domain oscilloscopes
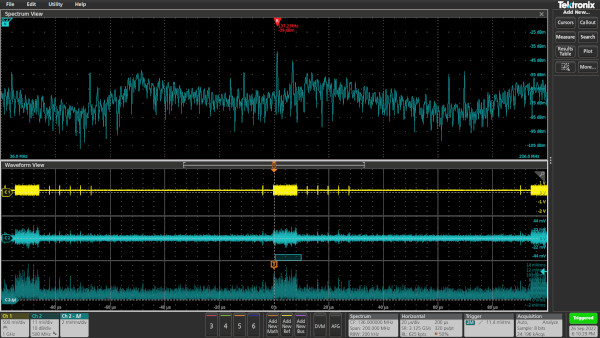
To root out sources of radiated emissions that lead to EMI issues, it's critical to identify the makeup of the emissions. Next, one must identify the aggressors and the coupling mechanisms. Using a mixed domain oscilloscope like the 4, 5 or 6 Series MSO with Spectrum View, one can capture a synchronized view of spectrums and time domain waveforms for fast identification of the culprits.
- Any analog channel can be viewed as a waveform, spectrum, or both
- Plot and trigger on changes in RF frequency or magnitude
- Spectrums and time domain waveforms are synchronized to correlate RF and time domain events for faster identification of root cause
- Spectrum controls such as center frequency and RBW are independent of time domain controls, allowing optimization of spectrum and waveform displays
Step by Step EMI Troubleshooting with 4, 5 and 6 Series MSO Oscilloscopes Application Note
Characterizing Self-Generated EMI for Wireless and IoT Products Application Note
Featured Content
New - EMCVu, an all-in-one EMI/EMC pre-compliance software solution
Video
Engineers now have a fast, easy, accurate and affordable way to determine if your new product designs are ready to submit to the test house. This video covers new EMCVu features, including: push button support for multiple standards, automated multiple measurement/multiple format reporting, ambient noise calibration and comparison, harmonic markers and faster scans using peak detector and spot measurements with quasi-peak and average detector failures.
Low Cost EMI Pre-compliance Testing using a Spectrum Analyzer
Application Note
This application note describes how you can use a general-purpose spectrum analyzer to perform EMI pre-compliance checks for radiated emissions and conducted emissions, to help identify major issues before sending your design to a compliance lab.
Full EMI Compliance Chamber vs Tektronix Spectrum Analyzer
Video
In this video we compare EMI compliance results obtained using a full Compliance Receiver set-up versus a low-cost approach using a Tektronix RSA Spectrum Analyzer. You’ll see how these results correlate for unintentional radiator emissions tests and a CISPR 11 EMI conducted emissions tests in and out of the EMI chamber. Performing a pre-compliance test using the RSA Spectrum Analyzer series can assist you in detecting problems that you can address prior to a compliance test, saving you time and money by ensuring you pass expensive compliance tests the first time.
Frequently Asked Questions (FAQ)
What is EMI?
Sometimes called radio frequency interference (RFI), electromagnetic interference (EMI) occurs when electromagnetic energy disrupts the operation of an electronic device. The source of EMI can be man-made, such as other electrical devices like switch-mode power supplies, personal computers, or naturally occurring, such as electrical storms, solar radiation, or even cosmic noises.
What is EMC?
Electromagnetic compatibility (EMC) is the ability of a device to operate as intended in an environment with other electrical devices or sources of EMI without affecting those other devices. A device is said to be EMC-compliant when it does not influence the electromagnetic environment to the extent that other devices and systems are negatively affected.
What is EMI and EMC testing?
To ensure compliance with EMI and EMC national and international regulations, many companies employ the services of a specialized testing facility. Since these tests are expensive—even if the product fails—several companies perform EMC pre-compliance testing in-house. If they have a sophisticated enough lab, companies may also perform EMC compliance testing in-house.
What is EMI pre-compliance testing?
What are the types of EMC tests?
When electronics are submitted to EMC testing labs, there are many types of EMC tests these labs run. Generally speaking, EMC testing is divided into two categories: immunity testing and emissions testing.
Immunity testing
Immunity testing is the process of transmitting RF energy onto a device under test (DUT) (also referred to as equipment under test or EUT) to determine if the DUT/EUT operates correctly when in such an environment.
Emissions testing
Emissions testing is the process of measuring the RF emissions – both radiated and conducted – of a DUT/EUT to determine if its emissions levels do not exceed the limits defined by the appropriate standard. Emissions testing includes both radiated and conducted emissions tests.
- Radiated emissions: Radiated emissions are the intentional and unintentional release of electromagnetic energy from an electronic device. A radiated test is performed to ensure emissions emanating from the DUT or EUT comply with the applicable limits.
-
Conducted emissions: Conducted emissions are the coupling of electromagnetic energy from a device to its power cord. Like radiated emissions, the allowable conducted emissions from electronic devices are controlled by different regulatory agencies and testing is performed to ensure emission levels are below the applicable limits.
-
What types of EMC testing labs are there?
EMC-compliance tests are commonly done off-site prior to the production of a device. Open-air test sites, or OATS, are the reference sites used for most standards. They are especially useful for emissions testing of large equipment systems. However, RF testing of a physical prototype is more often carried out indoors, in a specialized anechoic chamber. Types of chambers include anechoic, reverberation, and the gigahertz transverse electromagnetic cell (GTEM cell).
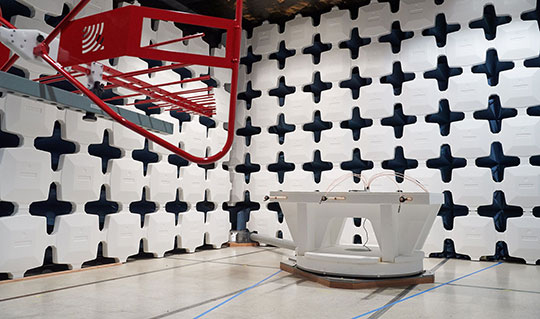
What is EMC testing procedure and average pass rate?
Roughly 50 percent of products pass their first EMC compliance test when pre-compliance isn’t considered, so it’s essential to understand the process and standards a device is tested to in order to increase your chances of success.
- Know your standards: There are a variety of EMC standards that specify test procedures and limits for radiated and conducted emissions. These vary by country and type of equipment under test. The first step in testing is determining which standards apply to your product, and researching the testing procedures and limits required for compliance.
- Conduct pre-compliance EMC testing: EMC compliance testing can take up to two weeks to complete—not including the time it takes to get your product into the test queue—and can cost up to $20,000 per submission. A failure in EMC compliance can result in expensive redesigns and product launch delays. And since nearly 50 percent of products fail their first EMC compliance test when pre-compliance isn’t considered, it’s likely that you’ll need to repeat your visit to the test house, multiplying costs over time.
- Find an EMC testing lab: Once a product has gone through pre-compliance testing and passed the test with a sufficient margin, it needs to be formally certified by an EMC testing lab. Accredited labs are the gold-standard for EMC testing and choosing an accredited lab is always recommended—though not necessary—to ensure your device is ready to go to market. There are, however, some instances that require certification from an FCC-accredited lab, including devices that fall under the 'certification' authorization procedures.
What products are needed for EMI and EMC testing?
The goal of EMC pre-compliance testing is to mimic the compliance test set up within an acceptable margin to uncover potential problems and reduce risk of failure prior to the expensive compliance test. EMC pre-compliance testing typically involves:
- Spectrum analyzer with quasi-peak detector
- Preamplifier (optional)
- Antenna with non-metallic stand for radiated emissions
- Line impedance stabilization network (LISN) for conducted test
- Power limiter for conducted test
- EMC near-field probes for diagnostics (optional)
- Oscilloscope with frequency and time correlation capabilities to assist in debugging (optional)
- EMC testing software
How to set up a pre-compliance EMC test lab?
When selecting a test site, rural areas, conference rooms, and basements are good options because they minimize external signals that might mask the DUT emission levels you are trying to measure. Other considerations for improving accuracy include having a good ground plane and reducing the number of reflective objects around the test area.
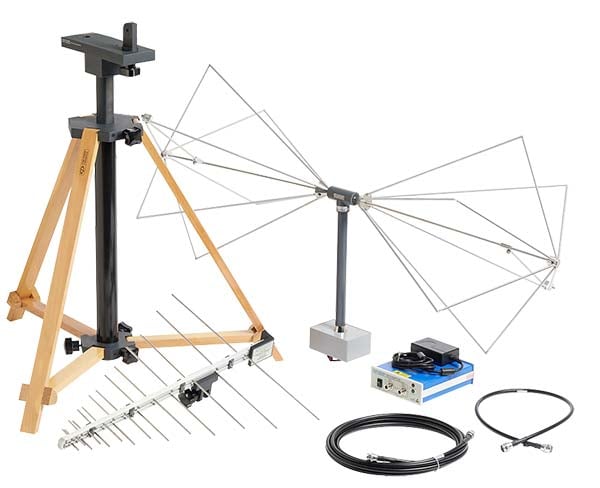
How to pass EMC compatibility testing?
EMC pre-compliance testing is a fast and affordable way to ensure products pass EMC tests the first time In the early development stages, design-for-EMC techniques are combined with diagnostics to build products with low susceptibility to both external and internal interference. Later in the development cycle, pre-compliance testing is used to catch compliance problems and improve the probability of a successful first pass of full EMC-compliance testing.
Additional benefits of pre-compliance EMC testing, include:
- Detects errors early, fixing potential issues
- Lowers testing and design costs
- Projects become more agile
- Lowers risk of failure and leads to assured compliance
- Addresses both over and under design and engineering
- Full EMI Compliance Chamber vs Tektronix Spectrum Analyzer