Fuel cells directly convert the chemical energy in methanol or hydrogen fuel into electricity. They hold great promise as power sources because they deliver more energy than batteries of the same size and weight and their only byproduct is water vapor
Fuel cells have been used for years in space and specialty applications; today, there is strong interest in commercializing fuel cell technology, especially from governmental organizations and automakers seeking a zeroemission power source. Fuel cells are now predicted to replace traditional power sources in the coming years—from tiny fuel cells in cell phones to high powered ones in race cars. However, to make fuel cells commercially viable, it is necessary to perfect the manufacturing of their components.
The bipolar plate is one critical component of Proton Exchange Membrane (PEM) fuel cells. A bipolar plate acts as both anode for one cell and cathode for the adjoining cell. It is porous, so it also provides a means of feeding oxygen to the cathode and fuel gas to the anode. This is an improvement on earlier PEM fuel cell designs that use distinct cathodes and anodes separated by electrolyte. (See Figure 1.)
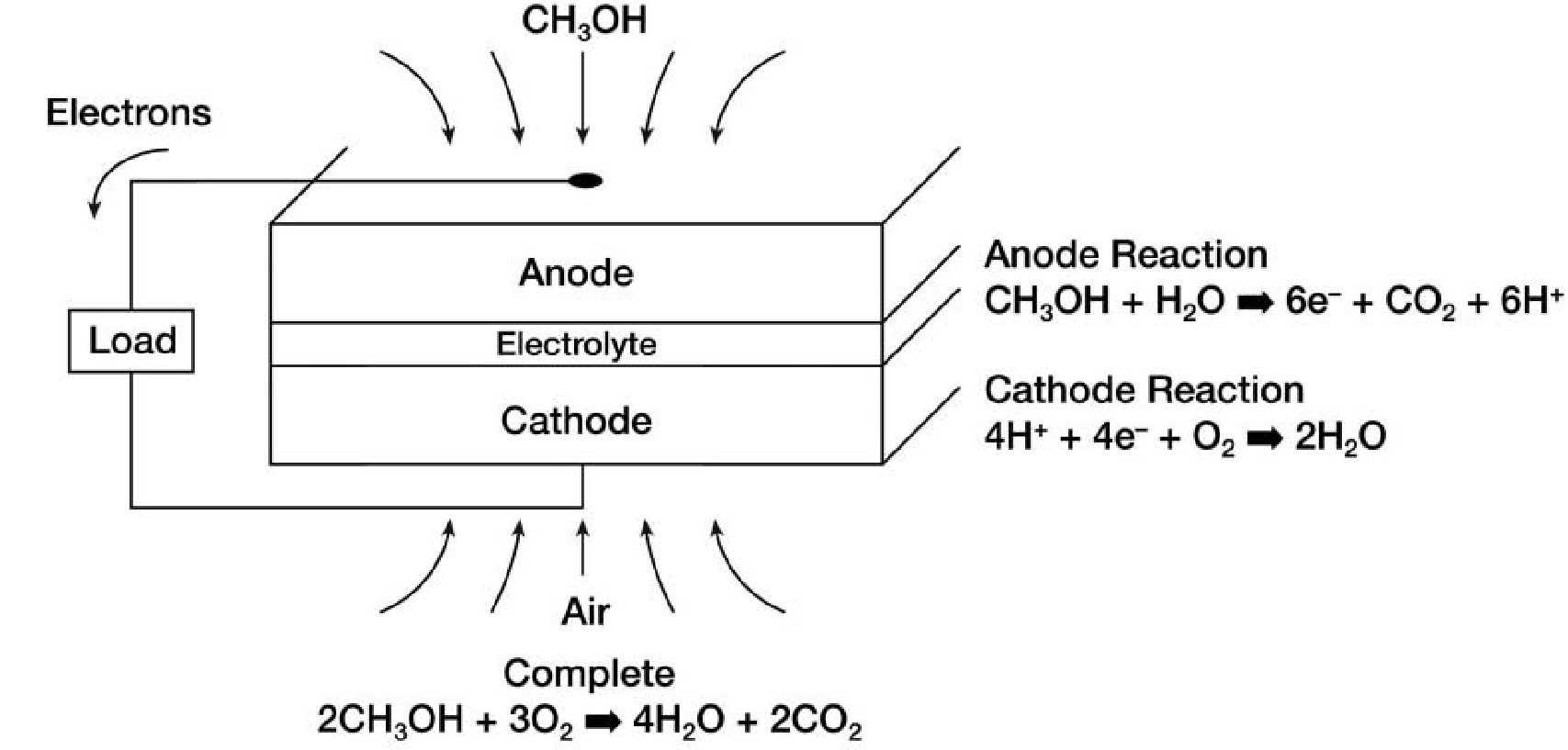
A typical fuel cell is constructed in layers of alternating anodes and cathodes. Individual cells are arranged in a stack and electrically connected. A bipolar plate design differs in that the anode and the cathode of adjacent cells form a shared bipolar electrode structure, reducing ohmic losses of the cell connections. In addition, the bipolar electrodes are rough and porous, maximizing the area for interaction and increasing the rate of fuel feed. As a result, bipolar plate fuel cells produce more current in a smaller width stack.
To reduce the cost of manufacturing bipolar plates, many companies have turned to graphite composites. These electrically conductive materials can be compression- or injection-molded into complex shapes. Compared to other bipolar materials, graphite composites have the advantages of low density, greater corrosion resistance, and ease of mass-manufacturing. However, if a thermoset bipolar plate is to work efficiently and have an acceptable service life, it must meet many demanding performance criteria.
One critical performance factor is the electrical conductivity of the bipolar plate. The better the electrical transport of a bipolar plate, the fewer plates are required to produce a given power output. This leads to a smaller fuel cell and lower cost, which are key features for market acceptance.
Test Requirements
Quantum Composites Inc. (Bay City, Michigan and North Kingsville, Ohio) has been manufacturing highly conductive composites since 1993 and bipolar plate materials since 1998. Quantum engineers wanted to test bipolar plate materials in order to identify materials and processes that gave the best results.
The company had been using a four-point probe test system as their primary research tool. While this tool supplied excellent measurement results for near-surface and surfacerelated electrical properties of bipolar plates, it could not provide the same insight into electrical characteristics deep inside the bipolar plate. Recently, Quantum engineers began to focus on a technique called through-plane measurement of electrical conductivity as a means of screening materials for desired characteristics, as well as for quality control testing.
Due to the time and cost of testing an entire fuel cell stack, Quantum engineers wanted a way to test individual bipolar material samples in a way that would be predictive of the performance of the material in a fuel cell.
Material conductivity could be easily calculated from measurements of the resistance. However, the development of the test apparatus was more complex. In a typical fuel cell, the stack of bipolar plates is held under pressure to seal the interfaces. Stress affects the electrical characteristics of the bipolar plate material; therefore, to measure the conductivity of a bipolar plate, a sample must be placed under pressure. Quantum experts solved this problem with a bench press that would simulate the operational conditions of a fuel cell stack.
Another test requirement was the ability to test samples at different pressure levels. The correlation between sample test results and actual in-stack performance has not yet been standardized. The complexity of a fully functional fuel cell makes this correlation difficult at the current stage of composite bipolar plate development. That’s why the tester needed the flexibility to accommodate various pressures and sample sizes.
Test Method
No off-the-shelf test system met their requirements, so Quantum engineers developed their own test system. (See Figure 2.) Quantum contacted Keithley Instruments, Inc. (NYSE:KEI) for guidance on their unique electrical test needs and to obtain the instrumentation for low voltage measurements and current sourcing: the Keithley Model 2182 Nanovoltmeter and the Keithley Model 2400 SourceMeter® instrument.
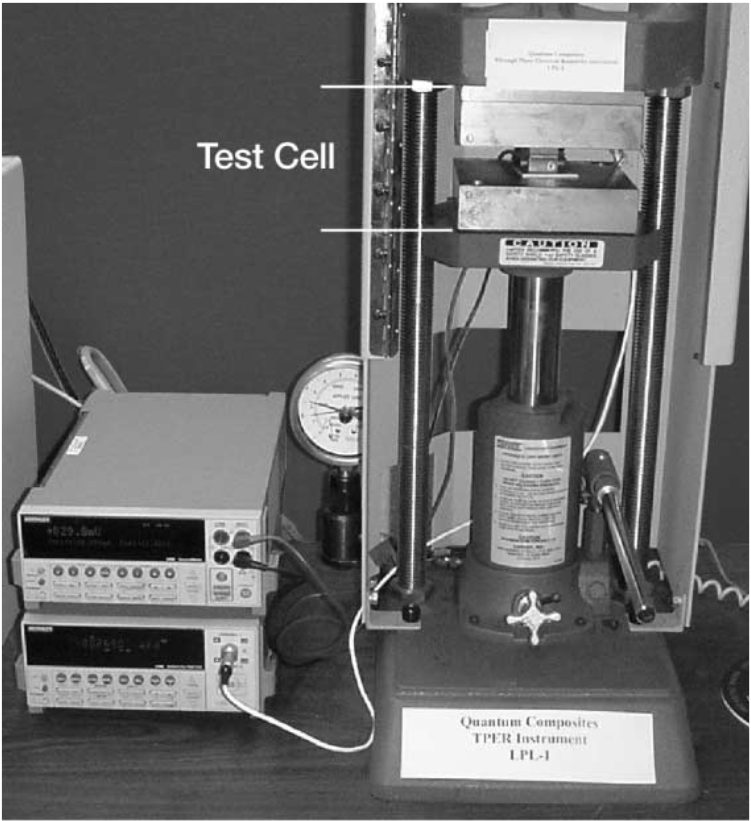
The through-plane test system speeded and simplified Quantum’s testing program. However, to ensure accurate and repeatable results, several measurement details demanded particular attention.
In the first step of the testing process, a one-inch by one-inch graphite-filled test sample was cut. The sample was placed between the two copper test electrodes. Figure 3 shows the test cell on the standard platens of the bench press.
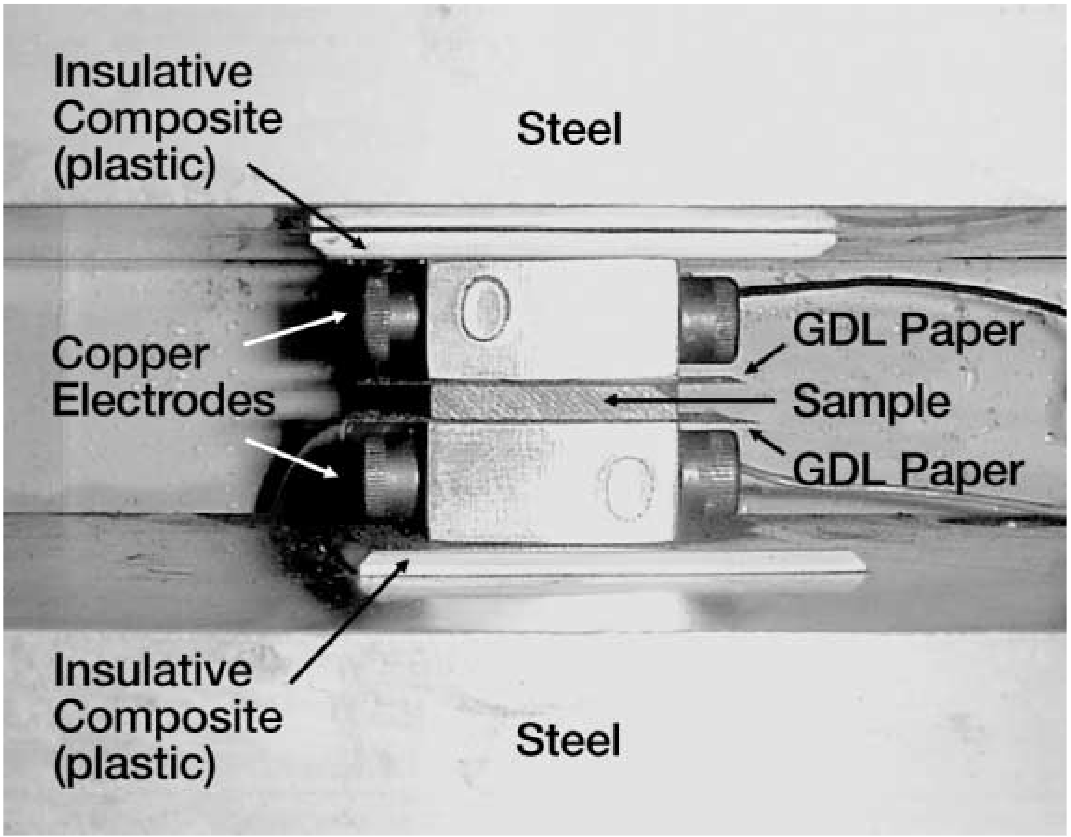
Sample resistance was on the order of 2mΩ, so poor test fixture contact could lead to measurement errors. Graphite Diffusion Layer (GDL) paper, typically Pyrofil® GDL paper (supplied by Mitsubishi Rayon Co., Ltd.), was added to improve electrical contact with the copper test electrodes. To improve electrical contact further, the test cell was placed under pressure.
Through experimentation, the researchers discovered that without GDL paper, it was difficult to create a good low resistance contact between the electrodes and the sample. For a one inch by one inch sample and 1000psi measurement, Quantum preconditioned the bipolar sample by cycling it three times at 1500psi. After preconditioning, a sample’s resistance was measured five times at 1000psi and the average value calculated.
Electrical Measurements and Calculations
The following equations were used to calculate sample resistivity and conductivity from the averaged resistance measurements:

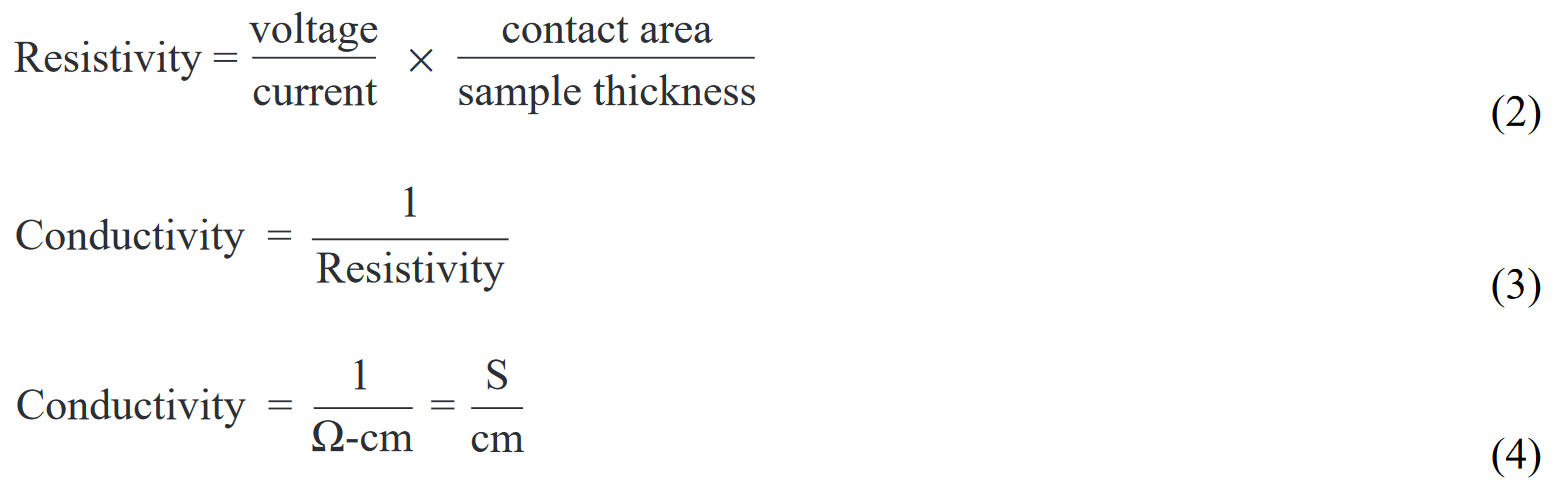
As Eq. 2 states, in order to calculate resistivity, it is necessary to know the contact area, sample thickness, and resistance of the sample. Resistance is determined by applying a current source to the sample, measuring the resultant voltage, and calculating resistance with Ohm’s Law. Test current, which must be kept low to avoid heating the sample, was typically around 100mA. For a 2mΩ sample resistance, this means the measured voltage was around 200µV. The four-wire (Kelvin) test method was used to reduce the effects of test lead resistance on measurement results. Even when this technique is used, thermoelectric EMFs (electromotive forces) in the measurement circuit can seriously affect low voltage measurement accuracy.
The current reversal or “Delta” measurement method is used to cancel the effects of thermoelectric EMFs. Each Delta reading is calculated from two voltage measurements made using a reversible current source – one measurement is made with current flow in the positive direction and the other is made with current flowing in the negative direction. (See Figure 3.) Keithley’s Model 2182 Nanovoltmeter, which has a built-in Delta function, was used for these measurements and calculations. The basic Delta calculation is:
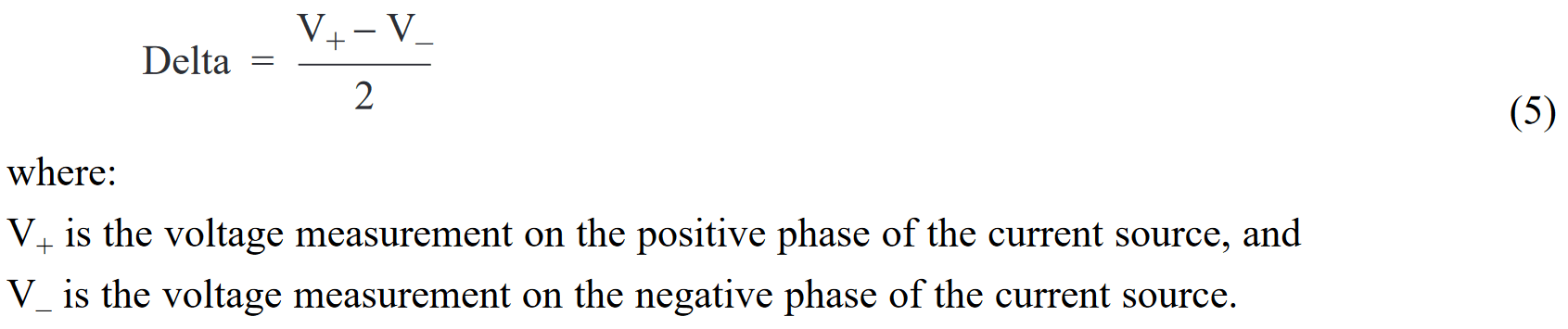
Practical Delta Measurements
The example in Figure 4 shows how a reversible current source and Delta measurements can be used to cancel the effects of a 10µV thermoelectric EMF. In Figure 4A, a constant 1mA is being sourced to a 0.1Ω device under test (DUT). Under ideal conditions, the nanovoltmeter would measure 100µV across the DUT (1mA × 0.1W). However, test connections and temperature fluctuations may generate thermoelectric EMFs in the measurement circuit. (The example in Figure 3 shows a constant 10µV thermoelectric EMF [VTHERM], but such EMFs drift with temperature.) For this example, the nanovoltmeter measures 110µV rather than 100µV, i.e., V2182 = VTHERM1 + VDUT1 = 10µV + 100µV = 110µV.
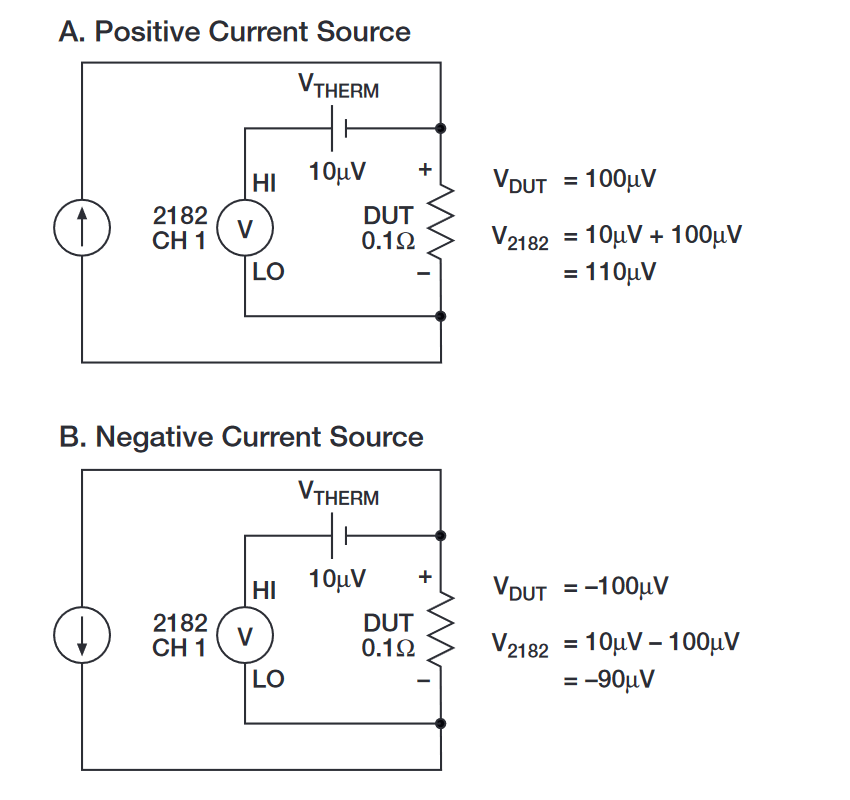
Figure 4B shows what happens when the current is reversed. The measurement result from the nanovoltmeter still includes the 10µV of thermoelectric EMF, but the voltage across the DUT is now negative. Therefore, the nanovoltmeter measures 90µV, i.e., V2182 = VTHERM2 + VDUT2 = 10µV – 100µV = –90µV.
As the example shows, neither of the nanovoltmeter readings is an accurate measurement of the voltage across the DUT. However, if the second equation is subtracted from the first equation and the result is averaged, the final result is 100µV, which is the actual voltage drop generated by the 1mA current through 0.1Ω resistance. The complete derivation of the Delta reading is:
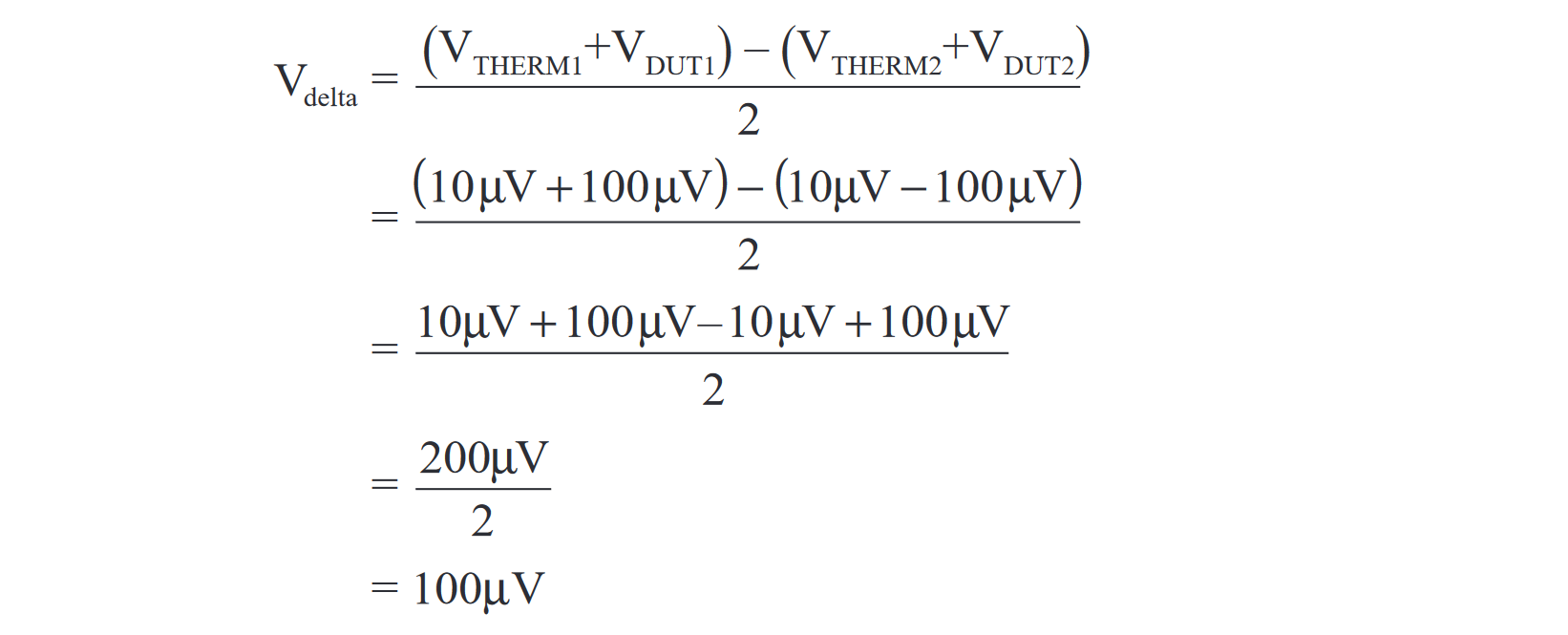
For random noise reduction and more accurate results, Delta measurements can be combined with a nanovoltmeter’s digital filtering functions using this equation:

where FiltV+ and FiltV- are filtered (averaged) voltage measurements on the positive and negative phases of the current source.
The downside to digital filtering is a longer measurement time, because multiple readings are required. However, filtering may not be required if random noise is not a problem. Generally, AC line noise, the prevalent problem in most measurements, can be minimized by using the appropriate measurement integration period. For example, the Keithley Model 2182 is optimized to provide low noise readings when its A/D converter is set for an integration period of one power line cycle (1PLC). At 1PLC (16.67ms for 60Hz power), current can be reversed after about 100ms. At these reading rates, the amount of noise induced by power lines should be insignificant. However, filtering can be used to reduce peak-to-peak reading variations.
The reversible current source used for Delta measurements should have a switching speed as good or better than the nanovoltmeter’s measurement speed. It is a good idea to characterize some bipolar plate materials at different levels of applied current to determine if there is any interdependence between applied current and the Delta measurements. To satisfy this requirement, Quantum engineers chose the Keithley Model 2400 SourceMeter® instrument, which can sweep rapidly through a range of bipolar source currents.
This instrument replaces the simple reversible current source illustrated in Figure 4. The nanovoltmeter performs the first voltage measurement (V+) while the SourceMeter instrument sources +1mA. The second voltage measurement (V-) is performed while sourcing 1mA: The equations and calculations for Delta measurement results are essentially the same as when using a simple reversible current source.
Figure 5 illustrates the hardware configuration for the SourceMeter/nanovoltmeter measurement application. When using the nanovoltmeter to perform Delta measurements, its rate must be set to 1PLC to optimize measurement performance. At 1PLC, Delta measurements will cancel thermoelectric EMFs to a level less than 15nV. The SourceMeter instrument’s speed must be set to FAST (0.01PLC).
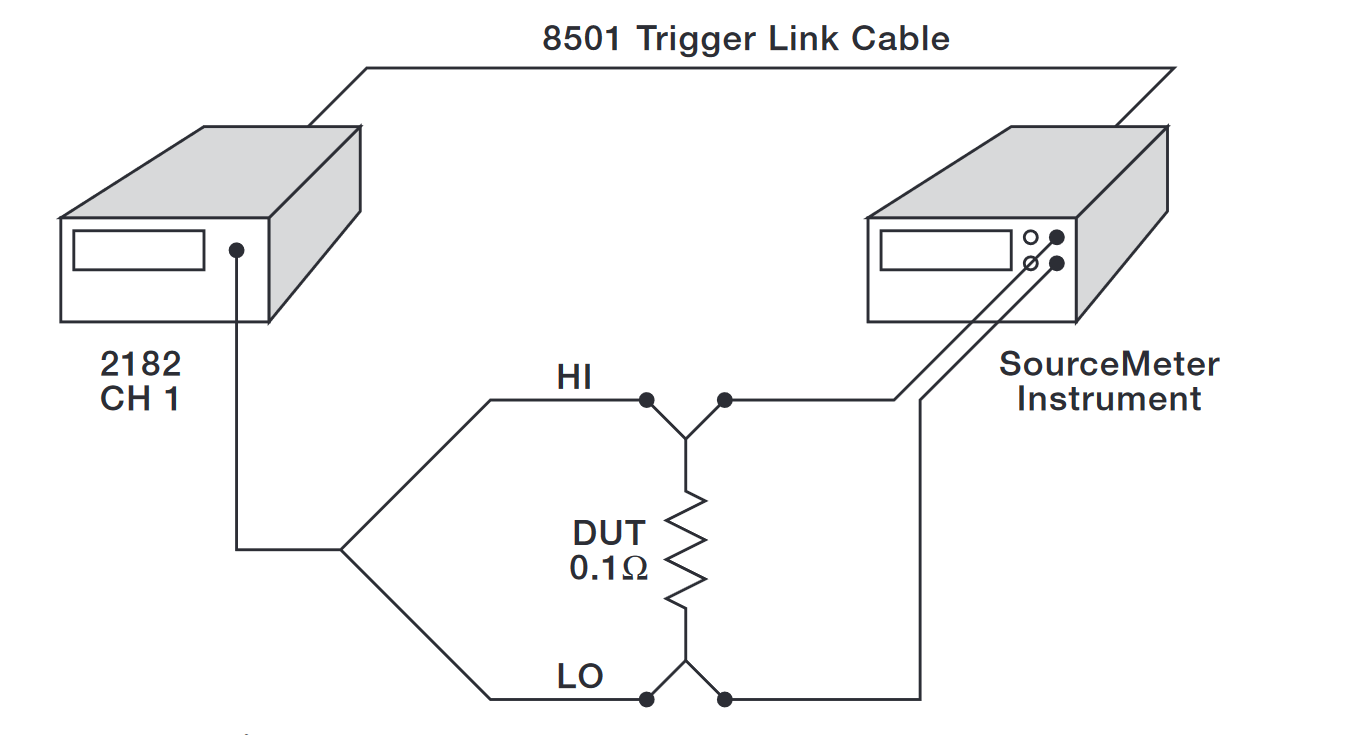
Results and Discussion
After Quantum researchers screened materials that could be net shape molded into large, thin bipolar plates with excellent thermal and corrosion resistant properties, throughplane electrical conductivity measurements were used to identify the formulas with the best characteristics. As noted earlier, a typical measurement is conducted at 0.1A on a one-inch by one-inch test cell. The results for one formulation were:
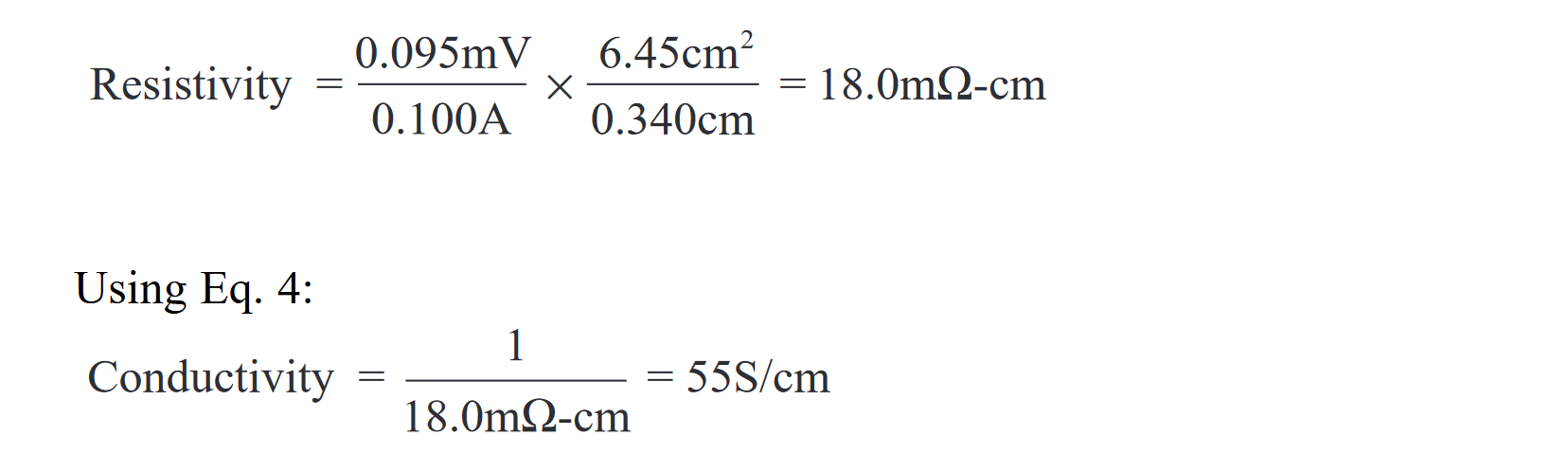
Ultimately, this screening process led to the development of a family of high performance conductive thermoset molding formulations that were patented under the PEMTEX® trade name. Depending on the specific formula used, these materials can be molded into plates of more than 100 square inches by 0.06 inches thick using compressionand injection-molding processes.
Along the way, the repeatability of through-plane electrical measurements was tested on two different formulas. The only variable in these data sets was replacement of the graphite paper. Results are shown in Tables 1 and 2. As the mean resistivity clearly shows, through-plane electrical measurements differentiate the performance of different formulas.
The data in Table 1 were collected by testing the same sample 20 times in the same position with the same graphite paper layer. The 20 cycles were performed by releasing and reclamping the sample to a nominal 1000psi. Errors in this test can be attributed to instrument measurements, pressure variations, and changes in paper performance as it degraded. Results were corrected for a graphite paper contribution of 0.0140mV (delta).
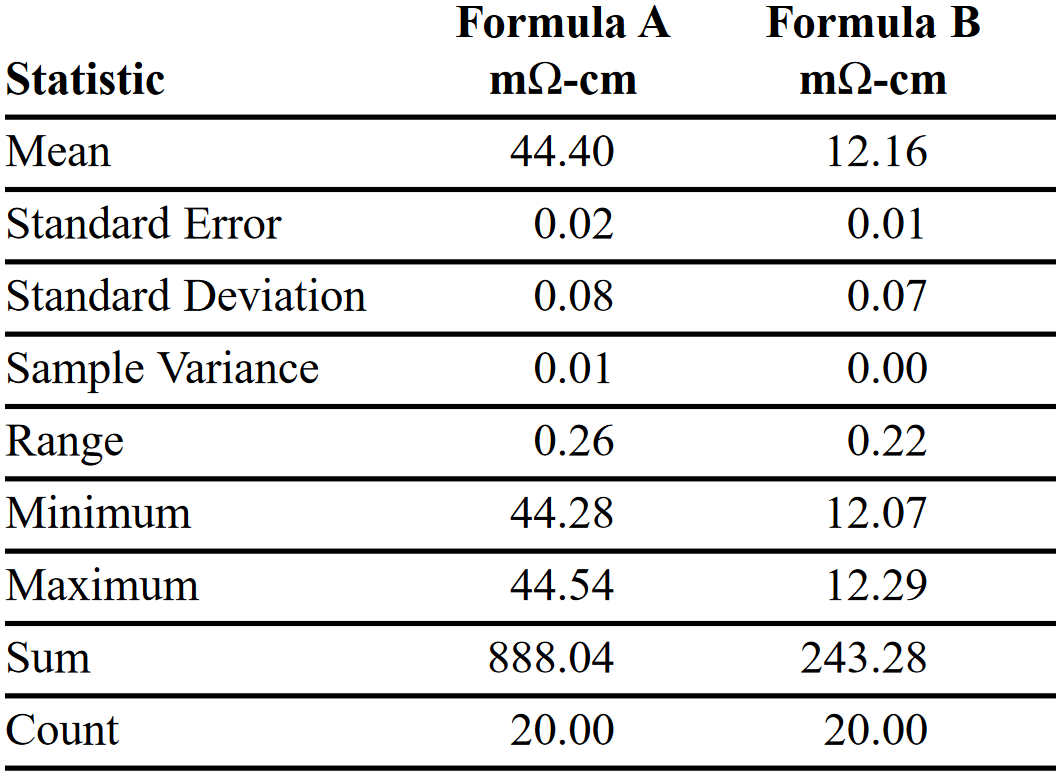
A second set of data was collected using samples of the same two formulas by testing each one 20 times in a row, but replacing the used graphite paper with new paper between pressure cycles. Both Formula A and B samples were pre-conditioned as described previously. This data set shows an increase in the standard deviation. This is attributed to errors arising from sample position, pressure differences, graphite paper variations, instrument measurements, and operator performance. Nevertheless, the mean conductivity values closely match those in Table 1 for the measurements made using the same graphite paper throughout the test cycle.
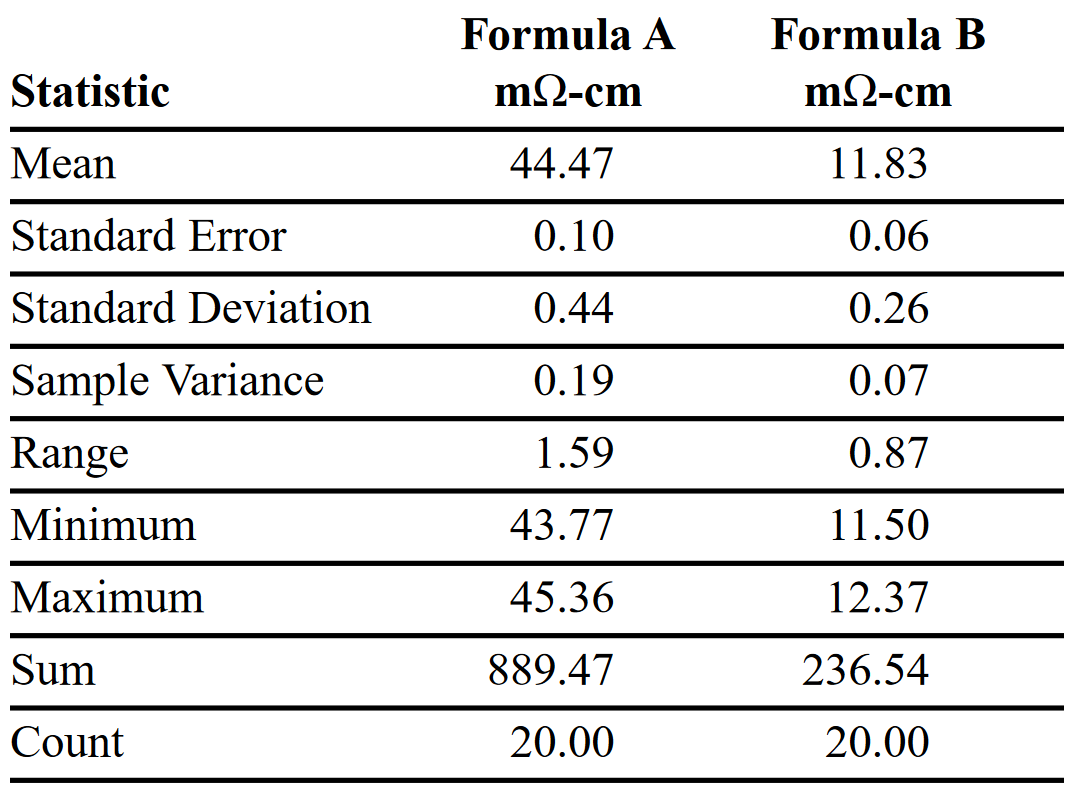
The final repeatability test involved placing samples of four different formulas in the cell and determining if any drift occurred over one hour. Data in Table 3 illustrates the electrical and physical integrity of the instrumentation. In one hour, the drift for the four different samples averaged 0.0006mV (delta). Unlike many other instruments, no long electrification time is needed before a result can be recorded. After pressure was applied and the electrical sweep was started, a stable voltage Delta occurred in about 5–10 seconds. All the samples had less than 0.010mV (delta) drift during the one-hour soak.
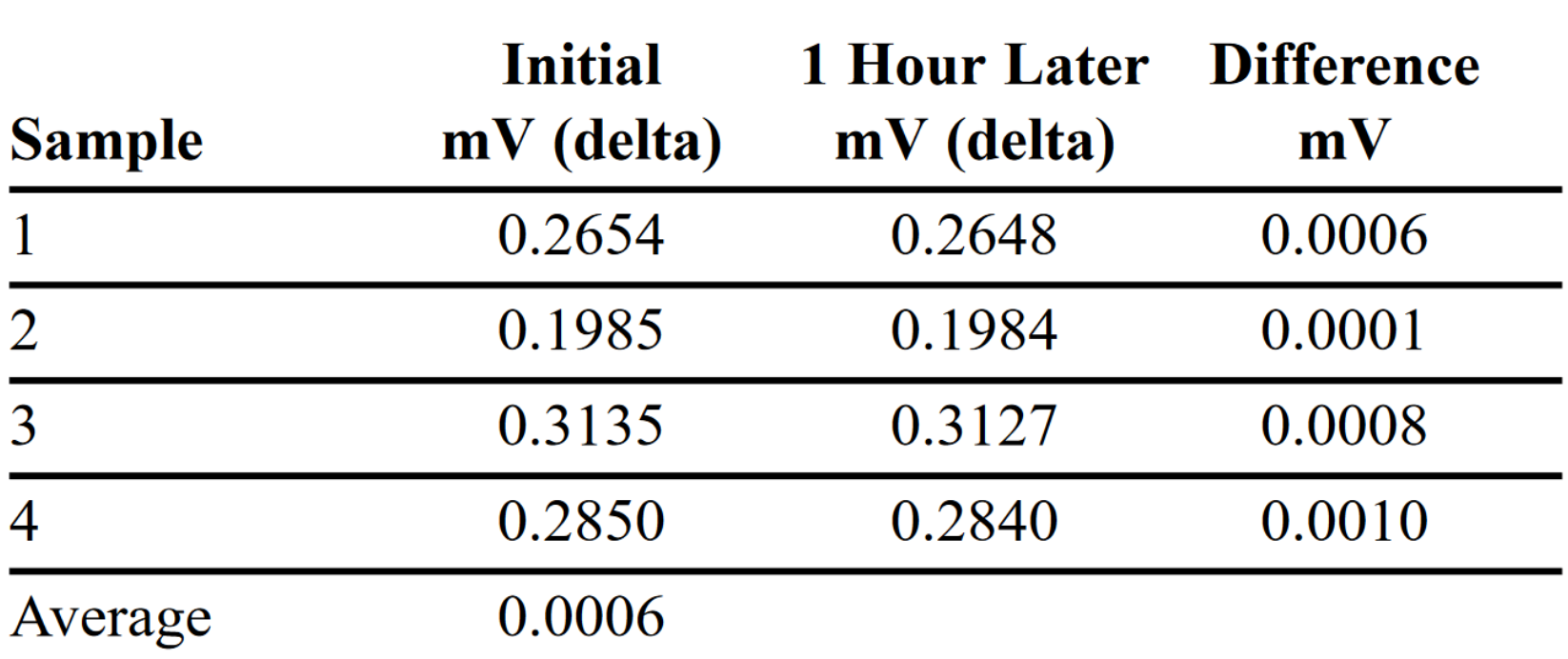
Although the measurement precision of the through-plane electrical test system can be determined, absolute accuracy is another matter because there is no suitable standard against which to compare it. Durable and homogeneous bipolar-plate material standards are very difficult to achieve with graphite-filled composites. To verify instrument performance/ accuracy, Quantum established a “comparative standard” material sample that has been repeatedly measured since the testing system was installed. This comparative standard is measured periodically to make sure the instrument is performing consistently. This helps determine if there has been any drift in the performance of the cell, pressure device, or electronics. Table 4 shows the results of randomly testing the standard on seven different dates over a period of six months. The results were directly read from the nanovoltmeter and corrected for GDL paper.
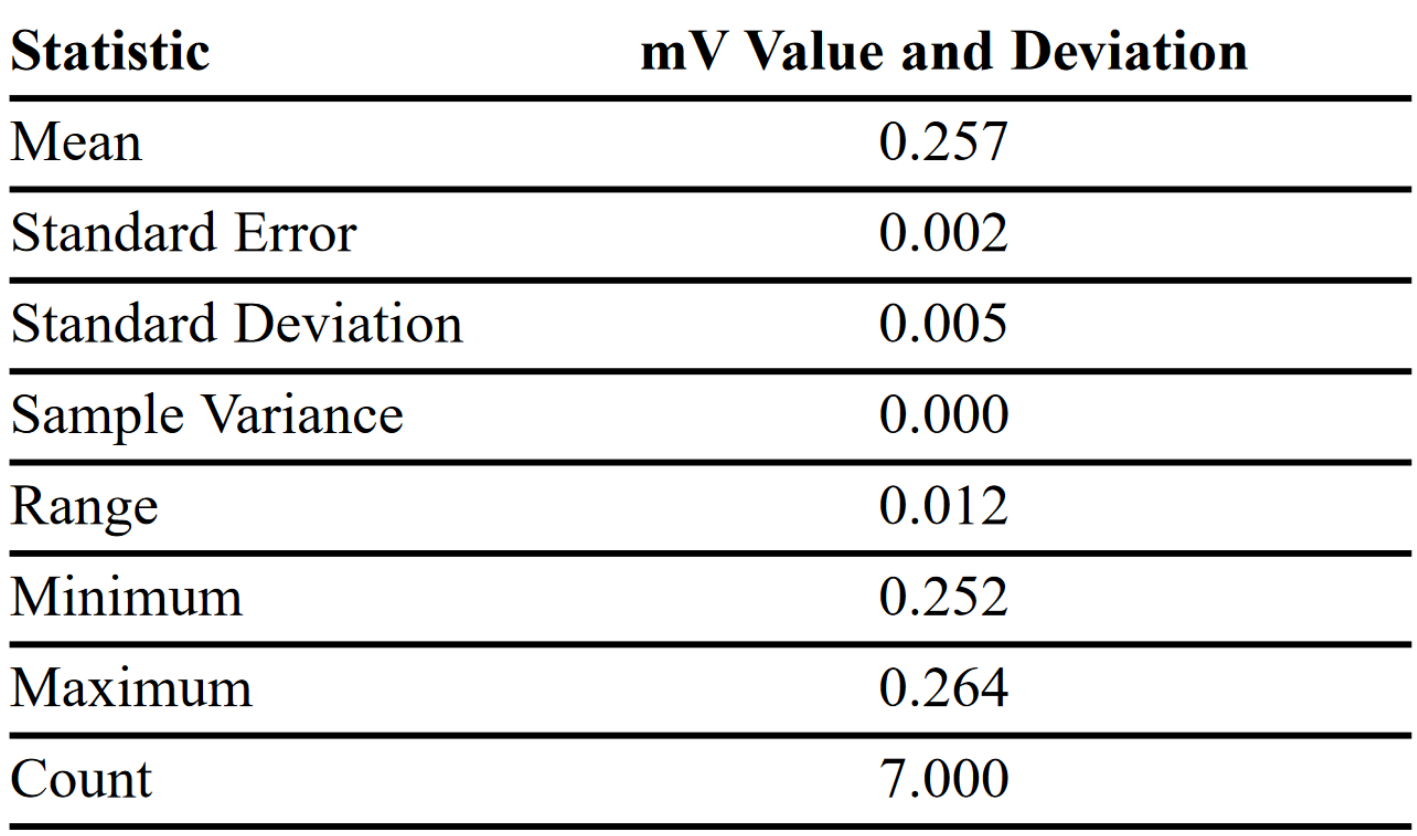
Data in Table 4 confirm the consistency and repeatability of through-plane electrical tester results. When monitored with an appropriate standard sample, this test method provides excellent measurement accuracy, allowing fuel cell developers to draw valid conclusions about bipolar plate material properties.
Application Results
Over several months of through-plane electrical testing, Quantum researchers collected data that led them to make bipolar-plate material changes that directly affect the critical performance parameters of fuel cell OEMs.
In addition, test data have enabled researchers to improve their models of electrical flow within bipolar-plates. This information has been used to improve formulations and equipment for material processing and bipolar plate molding. Ultimately, this has resulted in final products with better performance.
The industry must come to terms with the often-confusing (and sometimes conflicting) experimental procedures used to determine electrical properties of graphite-filled composite bipolar plates. As a result of its experience with through-plane testing, Quantum is currently working with the US Fuel Cell Council to define standard methods for measuring bipolar plate conductivity.
Other Applications
The technology and instrumentation developed by Quantum and Keithley can be applied to other products and production applications, such as ESD coatings and various graphite products. The through-plane electrical test system is not only simple to operate, but it provides its users with immediate feedback on a material’s performance.
Find more valuable resources at TEK.COM
Copyright © Tektronix. All rights reserved. Tektronix products are covered by U.S. and foreign patents, issued and pending. Information in this publication supersedes that in all previously published material. Specification and price change privileges reserved. TEKTRONIX and TEK are registered trademarks of Tektronix, Inc. All other trade names referenced are the service marks, trademarks or registered trademarks of their respective companies.
No.2399 7023KGW