Introduction
Signal integrity is a growing priority as digital system designers pursue ever-higher clock and data rates in computer, communications, video and network systems.At today s high operating frequencies, anything that affects a signal s rise time,pulse width, timing, jitter or noise content can impact reliability at the system level.To ensure signal integrity, it is necessary to understand and control impedance in the transmission environment through which the signals travel. Mismatches and variations can cause reflections that decrease signal quality as a whole.
Impedance tolerances are part of the electrical specifications for many of today’s digital system components, including Firewire, PCIe, SATA, DisplayPort and more. It is standard practice to use modeling tools to design high-speed circuits.Modeling hastens the design cycle and minimizes errors.However, modeled designs must be verified with hardware measurements, including impedance measurements, after the prototype is built.
The methodology of choice for measuring impedances is Time Domain Reflectometry (TDR), carried out using highperformance instruments such as the DSA8200 oscilloscope equipped with the 80E04 TDR sampling module. TDR permits the signal transmission environment to be analyzed in the time domain just as the signal integrity of data signals is analyzed in time domain.
What is Time Domain Reflectometry?
Time Domain Reflectometry (TDR) measures the reflections that result from a signal travelling through a transmission environment of some kind - a circuit board trace, a cable,a connector and so on. The TDR instrument sends a pulse through the medium and compares the reflections from the unknown transmission environment to those produced by a standard impedance. A simplified TDR measurement block diagram is shown in Figure 1.
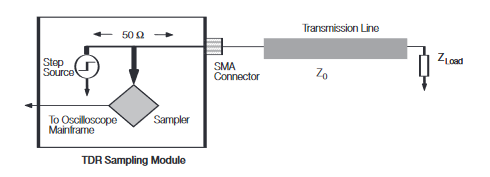
The TDR display is the voltage waveform that returns when a fast step signal is propagated down a transmission line. The resulting waveform is the combination of the incident step and reflections generated when the step encounters impedance variations.
The Reflection Coefficient: Doing the Math
The mathematical foundation of TDR measurements is elementary but important. Fundamentally, TDR measurements are based on a series of impedance ratios. Most TDR instruments will perform the necessary ratio calculations internally and display a numerical result.
TDR measurements are described in terms of a Reflection Coefficient, ρ (rho). The coefficient ρ is the ratio of the reflected pulse amplitude to the incident pulse amplitude:
ρ = | Vreflected |
Vincident |
For a fixed termination ZL, ρ can also be expressed in terms of the transmission line characteristic impedance, ZO and the load impedance ZL.
ρ = | Vreflected | = | (ZL - ZO) |
Vincident | (ZL + ZO) |
Now that we have the formulas, if we plug in numbers representing a matched load, a short circuit and an open load, we can see that ρ has a range of values from +1 to -1, with 0 representing a matched load.
When ZL is equal to ZO, the load is matched. Vreflected, the reflected wave, is equal to 0 and ρ is 0. There are no reflections:
ρ = | Vreflected | = | 0 | = | 0 |
Vincident | V |
A ZL reading of zero (0) implies a short circuit. The reflected wave is equal to the incident wave, but opposite in polarity. As seen below, the reflected wave negates part of the incident wave. The ρ value is -1.
ρ = | Vreflected | = | -V | = | -1 |
Vincident | V |
When ZL is infinite, an open circuit is implied. The reflected wave is equal to the incident wave and of the same polarity. As seen below, the reflected wave reinforces part of the incident wave. The ρ value is +1.
ρ = | Vreflected | = | V | = | 1 |
Vincident | V |
Figure 2 is an actual TDR display from a Tektronix Sampling oscilloscope. The traces clearly illustrate the math concepts summarized above.
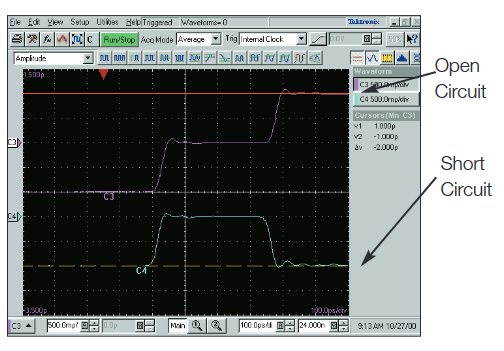
Calculating the Impedance of the Transmission Line and the Load
The characteristic impedance Z0, or the load impedance ZL, can be calculated with the value of ρ
ZL = | ZO * | (1+ρ) |
(1-ρ) |
With most of today's TDR-capable instruments, such as the Tektronix sampling oscilloscope, TDR measurements can be displayed with units of volts, ohms, or ρ (rho) on the vertical magnitude scale. The horizontal axis represents units of time, as shown in Figure 3.
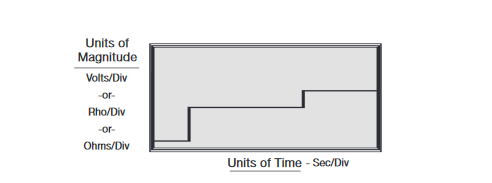
Other lumped and distributed effects can be observed and characterized with TDR techniques. Figures 4 through 8 illustrate idealized TDR results obtained with diverse types of impedance and terminations.
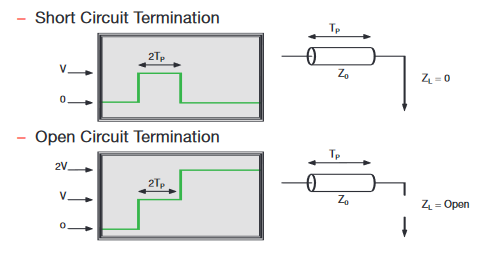
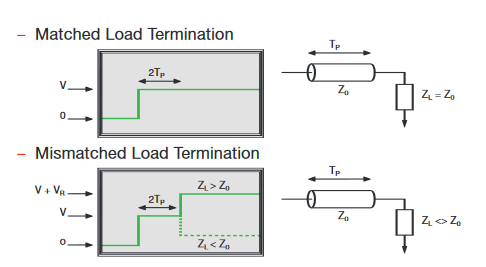
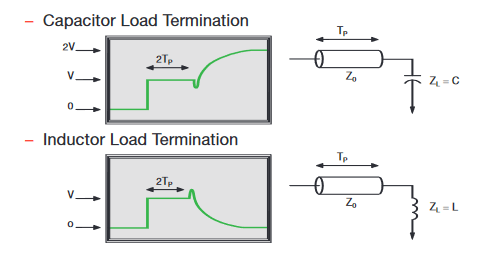
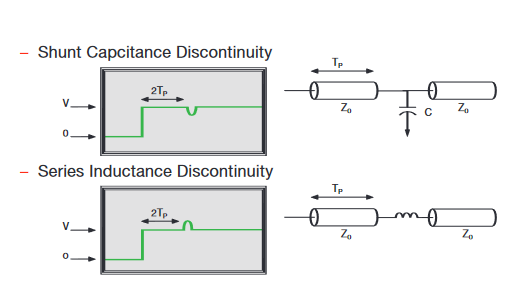
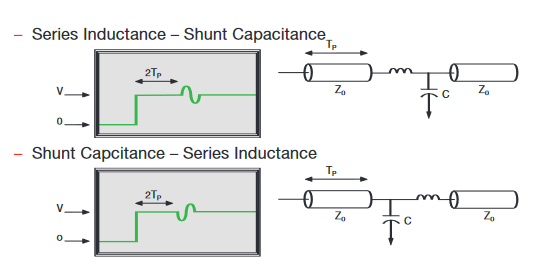
Looking at Real-World Circuit Characteristics
Typically, etched circuit boards have impedance-controlled microstrip and stripline transmission lines. Over the span of these transmission lines, components, vias, connectors and other “interruptions” create impedance discontinuities. These discontinuities can be modeled as inductors, capacitors and transmission lines.
The TDR waveform shows the effect of all the reflections created by all of the impedance discontinuities, as shown in Figure 9. The waveform is like a road map of the impedance variations across the trace. Now the waveform can be evaluated to determine how much the impedance deviates from the nominal value. Some TDR-capable instruments, such as the DSA8200 oscilloscope and 80E04 TDR sampling module, offer extended math functions that can calculate actual component values and the physical distance to points of interest along the transmission line.
In Figure 9, the waveform is the result of an ideal pulse traveling through a transmission medium. A TDR sampling module such as the 80E04 produces a very accurate, controlled pulse with a fast rise time and minimal aberrations. Imagine sending a typical data waveform down the same transmission path! The data pulse’s own aberrations would interact with the discontinuities in unpredictable ways. It’s a situation that lends itself to erratic, intermittent problems. Characterizing the environment with TDR measurements (and then correcting the discontinuities) can improve signal integrity significantly.
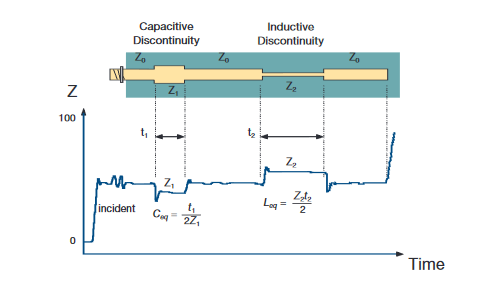
TDR Resolution Factors
We have established that TDR measurements can produce useful insights into circuit impedance and signal integrity. But all TDR solutions are not created equal. Several factors affect a TDR system s ability to resolve closely-spaced discontinuities. If a TDR system has insufficient resolution, small or closelyspaced discontinuities may be smoothed together into a single aberration in the waveform. This effect may not only obscure some discontinuities, but it also may lead to inaccurate impedance readings. Rise time, settling time and pulse aberrations can also significantly affect a TDR system s resolution.
Rise Time
A reflection from an impedance discontinuity has rise time equal to or-more likely-longer (slower) than that of the incident step. The physical spacing of any two discontinuities in the circuit determines how closely their reflections will be positioned relative to one another on the TDR waveform. Two neighboring discontinuities may be indistinguishable to the measurement instrument if the distance between them amounts to less than half the system rise time. The equation below summarizes this concept.
Pre - aberrations
Aberrations that occur prior to the main incident step can be particularly troublesome because they arrive at a discontinuity and begin generating reflections before the main step arrives. These early reflections reduce resolution by obscuring closely-spaced discontinuities.
Settling Aberrations
Aberrations, such as ringing, that occur after the incident step (Figure 10) will cause corresponding aberrations in the reflections. These aberrations will be difficult to distinguish from the reflections caused by discontinuities in the deviceunder-test (DUT). Note that aberrations in the TDR instrument's step generator and aberrations in the step response of its sampler have virtually the same effect.
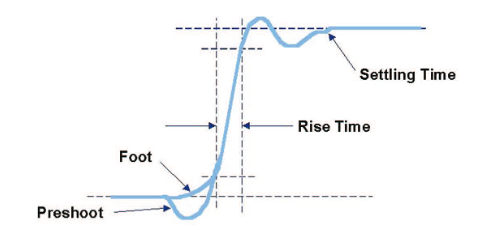
TDR Accuracy Factors
Many factors contribute to the accuracy of a TDR measurement. These include the TDR system’s step response, interconnect reflections and DUT losses, step amplitude accuracy, baseline correction and the accuracy of the reference impedance (ZO) used in the measurements.
Reference Impedance
All TDR measurements are relative; they are made by comparing reflected amplitudes to an incident amplitude. Modern TDR instruments perform all of the calculations to compare the incident and reflected amplitudes and show the results directly in rho or ohms. However, the process is still dependent on the accuracy of the reference impedance (ZO). For TDR applications, the Tektronix oscilloscope uses a highprecision 3.5 mm air line connector as a stable impedance reference for the calculation of rho and ohms. Connector impedance is measured relative to an external, traceable, precision air line during module calibration.
Step Amplitude and Baseline Correction
In general, modern TDR instruments measure and/or calibrate the incident step amplitude and, given the known step amplitude and baseline level, compute millirho and ohms. The Tektronix oscilloscope goes one step further by placing a known air line in the sampling module. It then monitors the baseline and incident step amplitude periodically. Thus, the system is automatically compensated, allowing for very repeatable measurements even if the step amplitude offset drifts.
Incident Step Aberrations
The most obvious problem caused by incident step aberrations is that the reflected step amplitude cannot be measured accurately, if the pulse does not settle in a time that is short relative to the line being measured. This type of error is only important for a DUT impedance that is significantly different than 50 ohms. In such a case, accuracy is highly dependent on the reflected step amplitude accuracy. Closer to 50 ohms, accuracy is more dependent on the reference impedance since reflections are very small.
A second type of aberration that can cause problems is the “foot” or pre-shoot that precedes the step. If the DUT has an open circuit at the end, this part of the step will reflect off the open circuit before the obvious rising edge of the step is in view. This will cause an error near the end of the line being measured.
A more subtle effect is caused by the low frequency step aberrations. These aberrations can appear as a slope in the trace even with a perfect 50 ohm termination in place of the DUT. This causes an offset in the 50 ohm level if the DUT is not measured in the same time period in which the reference impedance was measured.
Noise
Random noise can be a significant source of error when making measurements of small impedance variations. Fortunately, modern instruments can perform signal averaging to reduce the effects of random noise. The drawback in many instruments is that averaging can dramatically slow the processing speed, particularly if automatic measurements are being displayed. The Tektronix oscilloscope addresses this problem with its built-in multiple processors, which can share the processing workload.
Interconnect Accuracy and Reflections
If a long probe cable is used, it is prudent to measure the DUT impedance relative to the end of the cable in order to reduce the effect of cable loss. However, in this case, the impedance of the cable directly affects the accuracy of the measurement. The reference level will be shifted by the rho of the cable (ρcable) and the step amplitude incident on the DUT will be (1- |ρcable|). For maximum accuracy, these parameters can be measured and their impedance calculated.
Reflections from interconnect components and the probe-toDUT interface can also cause problems. The probe interface can create a large inductive reflection that must settle before an accurate measurement can be made. It is extremely important to keep the probe tip and ground leads short to minimize these problems.
Cable Losses
Cable losses in the test setup can cause several problems. While both conductor loss and dielectric loss can occur, conductor loss usually dominates. Conductor loss is caused by the finite resistance of the metal conductors in the cable which, due to the skin effect, increases with frequency. The result of this incremental series resistance is an apparent increase in impedance as you look further into the cable. So, with long test cables, the DUT impedance looks higher than it actually is.
The second problem is that the rise time and settling of the incident pulse is degraded by the time it reaches the end of the cable. This affects resolution and accuracy since the effective amplitude of the incident step is different than expected. This amplitude inaccuracy does not cause much error when the DUT impedance is close to 50 ohms, but for a larger or smaller impedance, the error can be significant.
Conductor loss can be minimized by using an extender cable to bring the sampling head closer to the DUT. If this is not possible, methods such as the Comparative Reflection technique can help resolve the issue. An example of this technique is as follows:
- Substitute an air line of known standard impedance for the DUT. Measure the actual impedance reading with this air line in place. This measurement provides an offset value that is used in the next step. The offset value quantifies the effect of the interconnect elements preceding the DUT.
- Add or subtract the offset value from all subsequent measurements on the DUT itself.
- The excellent linearity of TDR-capable instruments such as the DSA8200 oscilloscope ensures that the step signal experiences identical source, interconnect and sampler imperfections with either the standard or the DUT present.
The comparative reflection greatly improves the absolute accuracy of ρ and impedance measurements.
Controlling Rise Time
While in many cases the fastest rise time available is desirable, very fast rise times can, in some cases, give misleading results on a TDR measurement. For example, testing the impedance of a microstrip on a circuit board with a 35 ps rise time system provides excellent resolution. However, even the highest speed logic families in use today cannot begin to match the 35 ps rise time of the TDR step. Typical high-speed logic families such as ECL have output rise times in the 200 ps to 2 ns range. Reflections from small discontinuities such as stubs or sharp corners in the microstrip will be quite visible and may generate large reflections at 35 ps rise time. The same transmission line driven in actual operation by an ECL gate with a 1 ns rise time may produce negligible reflections.
This difference between measurement and reality could bethe beginning of a signal integrity problem. In attempting to correct the misleading impedance readings, you might compromise the environment that the real operational signals need. It is often preferable to see the transmission line s TDR response to rise times similar to the actual circuit operation.
Some TDR instruments provide a means of increasing the apparent rise time of the incident step. The Tektronix sampling oscilloscope implements filtering using a double-boxcar averaging technique, that is equivalent to convolving the waveform with a triangular pulse. The filtering is performed using live waveform math to show the filtered response in near real time. This technique provides fully “live” filtered waveforms, quickly responds to changes, and requires no additional calibration steps. The filtered waveform result corresponds very well with similar measurements made with an equivalent pulse from an external generator.
Differential TDR Measurements
Many high-speed designs are implemented with differential transmission lines. This approach offers many advantages, but does not eliminate the need to make TDR measurements to support signal integrity.
All of the single-ended TDR measurement concepts discussed so far also apply to differential transmission lines. However, they must be extended to provide useful measurements of differential impedance.
A differential transmission line has two unique modes of propagation, each with its own characteristic impedance and propagation velocity. Much of the literature refers to these as the odd mode and the even mode.
- The odd mode impedance is defined as the impedance measured by observing one line, while the other line is driven by a complementary signal.
- The differential impedance is the impedance measured across the two lines with the pair driven differentially. Differential impedance is twice the odd mode impedance.
- The even mode impedance is defined as the impedance measured by observing one line, while the other line is driven by an equivalent signal as the first.
- The common mode impedance is the impedance of the lines connected together in parallel, which is half the even mode impedance.
Tying together the two conductors in a differential line and driving them with a traditional single-ended TDR system, will yield a good measure of common mode impedance. However, common mode impedance is often less important than the differential impedance.
To provide true differential impedance measurements, the 80E04 TDR sampling module provides a polarity-selectable TDR step for each of two channels. With this approach, the differential system can actually be driven differentially, just as it will when the DUT is functioning in its intended application. The response of each side of the differential line is separately acquired and evaluated as a differential quantity.
Both sampler channels must have matched step response. The two steps must also be matched but complementary and the steps must be time-aligned at the DUT. The Tektronix oscilloscope meets these requirements by incorporating two acquisition and polarity-selectable TDR channels in a single sampling module containing a common clock source. The relative timing of the two step generators can be deskewed to precisely align the two steps at the DUT and remove any mismatch due to cabling.
With the TDR system set up with complementary incident steps, and using ohms units, adding the two channels yields the differential impedance. The individual traces give the odd mode impedance. If the line is not balanced, the two traces will not exactly match.
Deskewing the Step Generators
True differential TDR measurements require that both the stimulus and the acquisition systems be well matched in terms of timing and step response. The step response is fixed by the design of the system. The relative timing of the two channels, however, is usually adjustable. Both the acquisition timing and the TDR step timing must match to yield a valid TDR measurement. Notice, however, that the matching requirement lies at the DUT rather than the front panel of the instrument. Poor matching between the cables or interconnect devices and the DUT will skew the TDR steps in time when they arrive at the DUT, even if they are aligned at the instrument’s front panel, causing significant measurement error
The most efficient way to eliminate or reduce this problem is to minimize the interconnect length and use carefully matched cables. In the DSA8200 oscilloscope, the sampling head can be extended up to 2 meters from the mainframe without any performance penalty. This helps minimize cable lengths with associated mismatch, loss, dispersion and other errors
Deskewing of the acquisition paths is also very important, and in the DSA8200 oscilloscope, the timing of the step generators can also be skewed, relative to each other using the deskew control in the TDR setup menu. Setting the timing of the step generators by looking at the TDR response from the two channels can be difficult; the correct setting is not always obvious. However, the imbalance trace shows the effect of this timing mismatch in real time. Watching the imbalance trace makes adjusting the timing simple, since it displays the effects of the mismatch in real time.
This deskew operation is also important for the acquisition involved. In the DSA8200 oscilloscope, the two channels in one sampling module are inherently well matched because they are driven from a common clock source.
Static Discharge Precautions
High-bandwidth sampling heads are extremely static-sensitive. To ensure their continued performance in impedance and signal integrity applications, they require protection devices above and beyond those which suffice for conventional oscilloscopes. The following guidelines are essential when handling or using any high-bandwidth sampling module
- Cap sampling inputs when not in use
- Use grounded wrist straps of < 10 meg ohms when in contact with the module
- To prevent the possibility of probing a device that may have built up a charge, you should always discharge the device before probing or connecting it to the module. You can accomplish this by touching the probe ground lead or your finger (assuming you are using a wrist strap) to the point you want to TDR test. The SIU800 Static Isolation Unit uses a microwave relay to perform this function. With this unit, the DUT cable is connected to ground until a foot switch is depressed and the relay switches, connecting the DUT to the TDR input.
Probing and Interface Alternatives
The electrical interface from the coaxial 50 ohm cable environment to a circuit board microstrip can produce a localized disturbance in the ideal 50 ohm path to the tested device. It is desirable to make this disturbance as small as possible, but cost and convenience are also considerations. Here are some commonly used alternatives:
P6150 Probe and Tip Fittings
The P6150 probe is used by many manufacturers because of its convenience and off-the-shelf availability. This probe can be specified as a standard, repeatable part of a test station. The 50 ohm probe cable is constructed of an unusually flexible material.
SMA Board Launches
- Available from coax houses.
- Must be designed into and installed on the circuit board.
- Best interface for quality and repeatability
- Best for high-frequency testing.
Repeatability Issues
An important part of measurement accuracy is repeatability. A measurement made of the same part at different times should yield the same result. Although this repeatability does not guarantee accuracy, accuracy will be impossible without it. There are several factors that affect repeatability
- Probing and fixturing techniques and stability.
- Condition/quality of cables and connections.
- Measurement procedure.
- Instrument condition and calibration.
Application Example: Making a Coupled TDR Measurement on a USB Device
Background
Signal integrity requirements have expanded with the increased speed of USB. As a result, there has been an increased interest in impedance measurements and the effects of impedance variations within USB cables and devices. A Tektronix sampling oscilloscope, equipped with an 80E04 sampling module, offers a versatile solution for impedance measurements in support of signal integrity.
A high-speed USB connection is made through a shielded, twisted pair (differential) cable with a characteristic impedance of
Zodd = 45V (Zdiff = 90V )6 15%
Zeven = 60V (Zcm = 30V )6 30%
and a maximum one-way delay of 26 ns (TFSCBL). The D+ and D- circuit board traces, which run between a transceiver and its associated connector, should also have a nominal differential impedance of 90 ohms.
TDR Loading Specification
The AC loading specifications of a transceiver in the high-speed idle state are specified in terms of differential TDR measurements.
These measurements govern the maximum allowable transmission line discontinuities for the port connector, the interconnect leading from the connector to the transceiver, the transceiver package, and the transceiver IC itself. In the special case of a high-speed-capable device with a captive cable, the transmission line discontinuities of the cable assembly are also governed.
The following specifications must be met with the incident rise time of the differential TDR set to 400 ps. It is important to note that all times are "as displayed" on the TDR and hence are "round trip times."
Termination impedance (ZHSTERM) is measured on the TDR trace at a specific measurement time following the connector reference time. The connector reference time is determined by disconnecting the TDR connection from the port connector and noting the time of the open circuit step. For an "A" connector, the measurement time is 8 ns after the connector reference location.
For a "B" connector, the measurement time is 4 ns after the connector reference location. The differential termination impedance must be:
80Ω ZHSTERM 100 Ω
Through impedance (ZHSTHRU) is the impedance measured from 500 ps before the connector reference location until the time governed by the Termination impedance specification.
70 Ω ZHSTHRU 110 Ω
In the Exception Window (a sliding 1.4 ns window inside the Through Impedance time window), the differential impedance may exceed the Through limits. No single excursion, however, may exceed the Through limits for more than twice the TDR step rise time (400 ps).
In the special case of a high-speed-capable device with a captive cable, the same specifications must be met, but the TDR measurements must be made through the captive cable assembly. Determination of the connector reference time can be more difficult in this case, since the cable may not be readily removable from the port being tested. It is left to the tester of a specific device to determine the connector reference location by whatever means are available.
For more details about these TDR requirements and measurement conditions, see the Universal Serial Bus Specification standard, Revision 2.0.1
The DSA8200 oscilloscope with the 80E04 sampling module can display both the individual positive and negative TDR waveforms of a differential line. With this solution, the user can view reflection characteristics and directly measure the impedance of each conductor or the common mode of the differential line. This test system can also display the true differential measurements of both these lines and display them in ohms, providing the user with the required measurements to validate any USB device.
USB 2.0 Impedance Measurement Procedure
Connect the DUT
This connection can be accomplished with a breakout board that provides SMA connections on one end and a USB connector on the other. The breakout board should have an SMA connector for each of the differential lines, as shown in Figure 11.
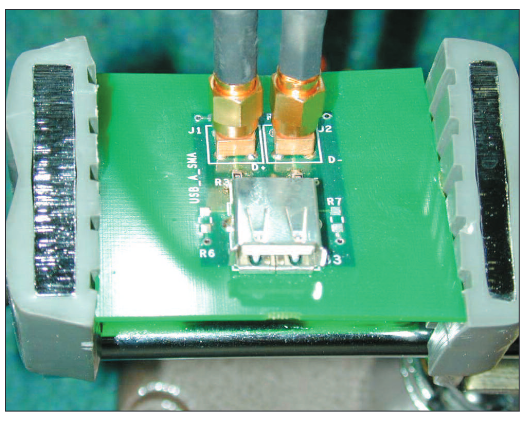
Connect the other end of the SMA cables to an 80E04 20-GHz TDR sampling module installed on the Tektronix oscilloscope. Be sure to follow strict static protection procedures when using any fast sampling module.
Turn on TDR Waveforms and Create Differential Step Pulses
In the TDR Setup menu:
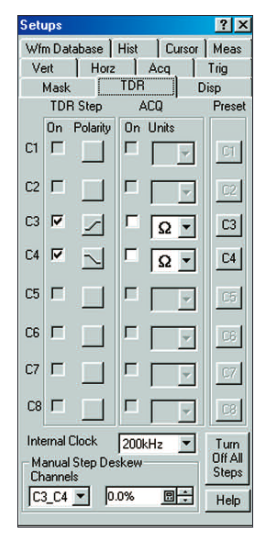
- Preset the channels that are associated. In this example it is Ch 3 and Ch 4, as shown in Figure 12.
- Select ohms (Ω) as the units to be displayed.
- Change the polarity of one of the channels to create a differential step.
You may also want to turn on Vectors in the Display menu and turn on Averaging from the Oscilloscope toolbar
Note that when you select negative polarity in the TDR menu, the step
generator produces a negative-going step. The sampling channel is not inverted. Also notice that when the selected units are volts, you can see the step go negative, but with rho and ohms units the step appears positive.
To understand this concept, remember the definition of rho: it is the reflected voltage divided by the incident voltage and, therefore, is not dependent on the sign of the incident step. This also makes sense physically: the sign of the reflection coefficient is an indicator of an impedance larger or smaller than the reference impedance, not a "negative impedance."
Locate the Area of Interest
Use the Horizontal and Vertical controls to display the resolution required. Here we have adjusted the display so that it is centered on the open USB connector (Figure 13).
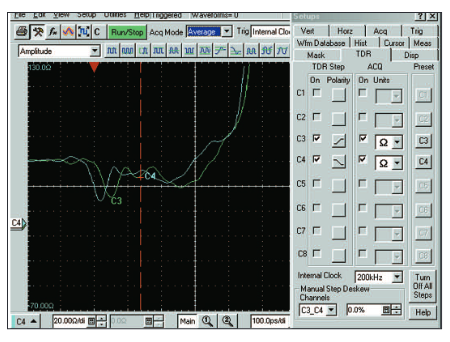
Adjust the Skew
Use the Deskew adjustment in the TDR Setup menu to deskew the two channels such that they are aligned at the USB connector where the DUT will be connected. The result is shown in Figure 14.
Create a Differential Filtered Waveform
- In the math menu (under Edit in the Windows¤ toolbar or the math icon in the oscilloscope toolbar), select Filter and enter the rise time desired for your test in the Filter Risetime menu (Figure 15). Typically 400 ps is used for USB devices.
- Mathematically add the two channels using the "+" button on the control panel window. To create the single differential waveform shown in Figure 14, turn on the math waveform and select Apply.
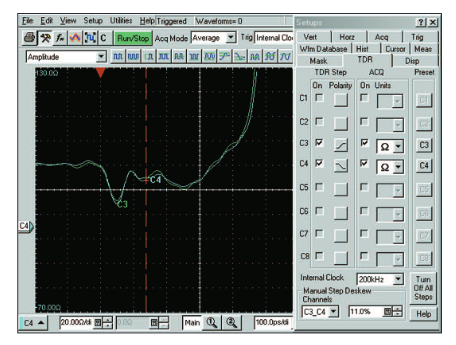
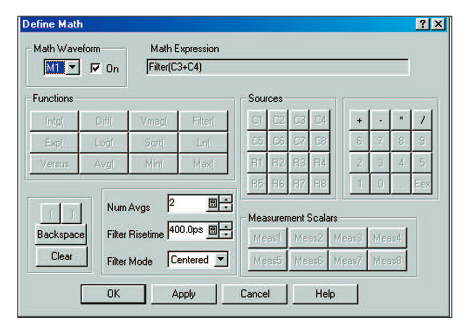
Use Automatic Measurements to Verify Tolerance Levels
- Select the Max and Min icons from the Amplitude Measurement Toolbar to turn on these measurements. (Make sure that M1 is the selected waveform.)
- Display the Measurement Setup menu (Figure 16) and create a Region using Gates for each measurement. In this example, 10% and 90% of the horizontal display will be used for the region to be measured. You may also want to turn on Annotations to see exactly where the measurements are being made.
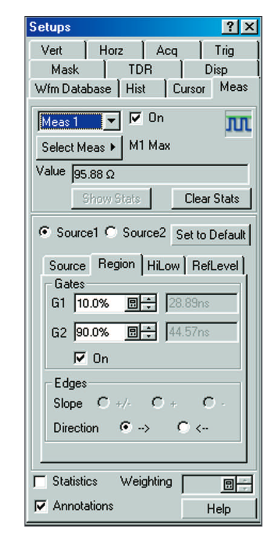
Verify Compliance with USB 2.0 Specifications
Figure 17 shows a TDR result with the Min and Max measuring within the tolerance specified by the USB differential specification, that is, 90% - 15%.
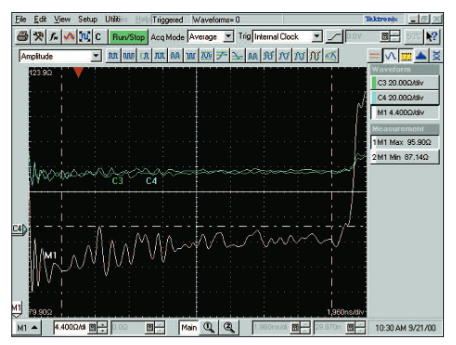
Now look at Figure 18. This is a TDR result with the maximum impedance exceeding the USB specification. This oscilloscope screen shot also includes a user mask set to outline the limits of the USB specification. With the mask lines in place, it is easy to spot violations that can affect signal integrity.
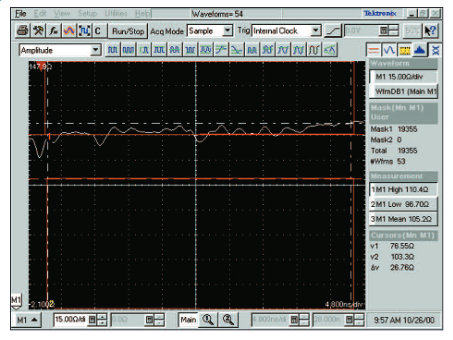
Conclusion
Signal integrity is an issue that grows more important with each |successive advancement in system clock and data rates. A key predictor for signal integrity is the impedance of the environment – cables, connectors, package leads, and circuit board traces – through which signals must travel. Consequently, impedance measurements have become part of almost every high-speed design project.
Time Domain Reflectometry is a convenient, powerful tool for characterizing impedance of single-ended and differential transmission lines and networks. A TDR instrument takes advantage of the fact that any change in impedance in a transmission line or network causes reflections that are a function of magnitude of the discontinuity
Modern TDR-capable instruments, such as the Tektronix Sampling oscilloscope, automatically compare the incident and reflected amplitudes to provide a direct readout of impedance, reflection coefficient and time for both common mode and differential impedance. In addition, waveform math functions built into the instrument can automatically display TDR results for a user-selected rise time, making it possible to see the response of a DUT to the signals it will encounter in its end application. By employing consistent procedures, static protection and good measurement practices, you will achieve stable and accurate TDR results.
Find more valuable resources at TEK.COM
Copyright © Tektronix. All rights reserved. Tektronix products are covered by U.S. and foreign patents, issued and pending. Information in this publication supersedes that in all previously published material. Specification and price change privileges reserved. TEKTRONIX and TEK are registered trademarks of Tektronix, Inc. All other trade names referenced are the service marks, trademarks or registered trademarks of their respective companies.
09/08 55W-14601-2