Introduction
One of the consequences of the rapid growth of the telecommunications, desktop computing, and network server markets is a burgeoning demand for switching power supplies and DC-to-DC converters. While these power supplies are typically inexpensive, a high level of quality must be maintained through careful production testing.
Highly accelerated stress screening (HASS) or “burn-in” is a common production step for switching power supplies designed for computers and servers. Extended environmental testing is performed to ensure the product will continue to function properly over its entire service life. It is not uncommon to age and monitor thousands of power supplies at once. When designing this type of test system, the biggest challenge is dealing with the high number of channels the system must monitor and the test system surroundings. Large numbers of switching power supplies can produce tremendous amounts of electrical noise, which can reduce the test system’s measurement performance significantly.
Test Description
High-end power supplies and DC-to-DC converters with outputs from 400W to 2000W are commonly found in many telecom and server applications. These devices typically have four to six voltage outputs that must be verified. Output voltages may vary from 3.3V to 48V, with one output terminal dedicated to 5V. To verify that the entire power supply is functioning properly, the manufacturer often monitors only the 5V output. This implies that all channels are measured during manufacture, but for the purposes of burn-in, only one output is monitored to reduce the number of channels needed for the test system. Reducing the number of channels monitored allows a test system to accommodate more power supplies during the testing cycle, reducing overall cost. Less expensive and less complicated power supplies found in PCs may have up to six outputs, while power adapters for laptop computers will have one output. As in the previous case, only one channel is monitored. The 5V output is monitored as the temperature in the environmental burn-in chamber reaches the upper and lower limits, and the power supply output is repeatedly cycled on/off.
Monitoring Voltage
Figure 1 is a simple schematic of a test for monitoring the voltage output of a power supply. A digital multimeter (DMM) would be connected in parallel with the load resistance to measure the power supply voltage. The load resistance is chosen to emulate the load resistances found in the final application, but may be chosen to reach full output capacity to perform stress testing.
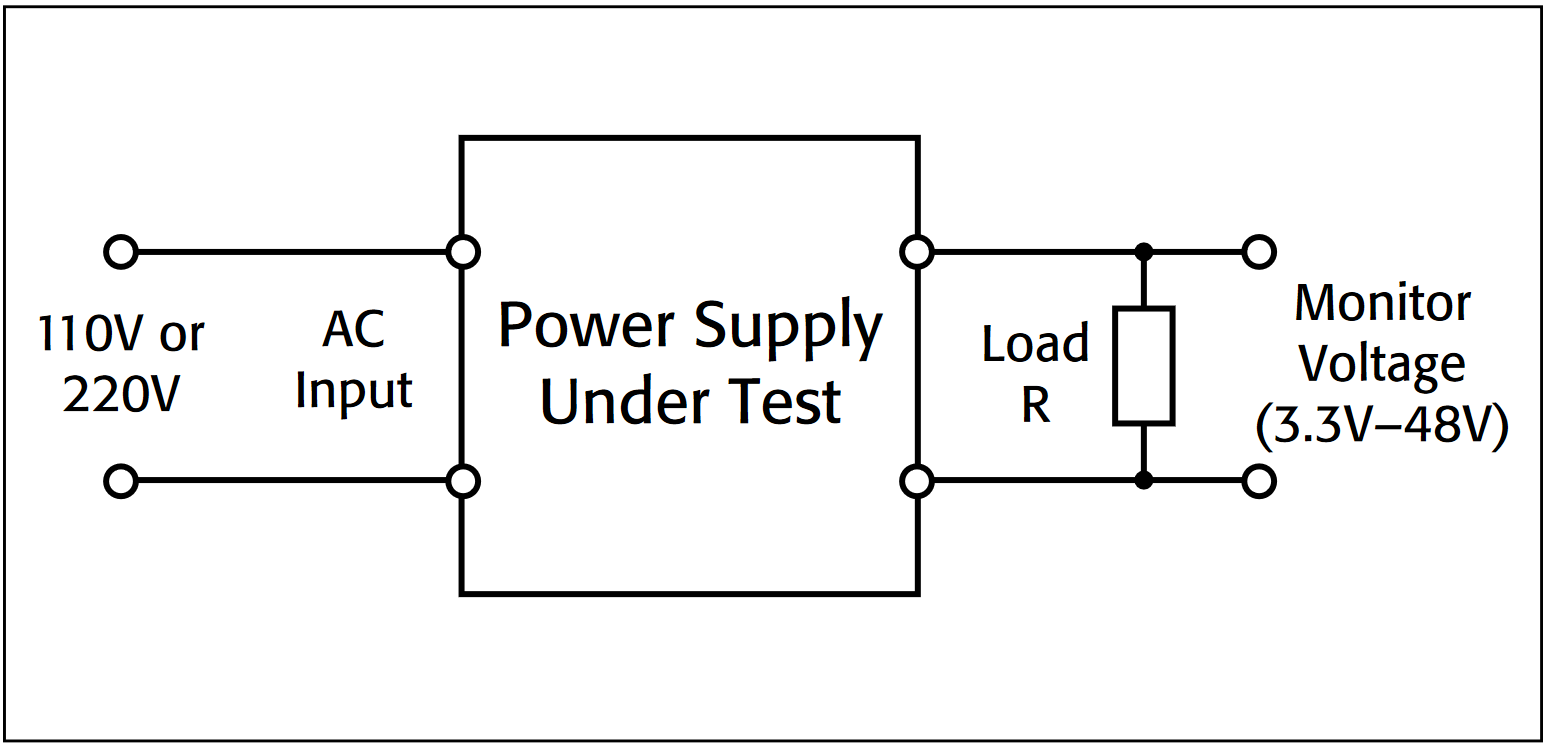
Output Cycling
To stress the power supplies being tested further, the output is repeatedly turned on and off. If a device is destined to fail, the failure will generally occur when the output is cycled. To capture failure data, the output voltage of each power supply is measured during each time the output is turned on, as shown in Figure 2. After the output is cycled 15 to 20 times, the output is left on and the power supply is left to continue aging. While the output is left on, the voltage is measured only occasionally.
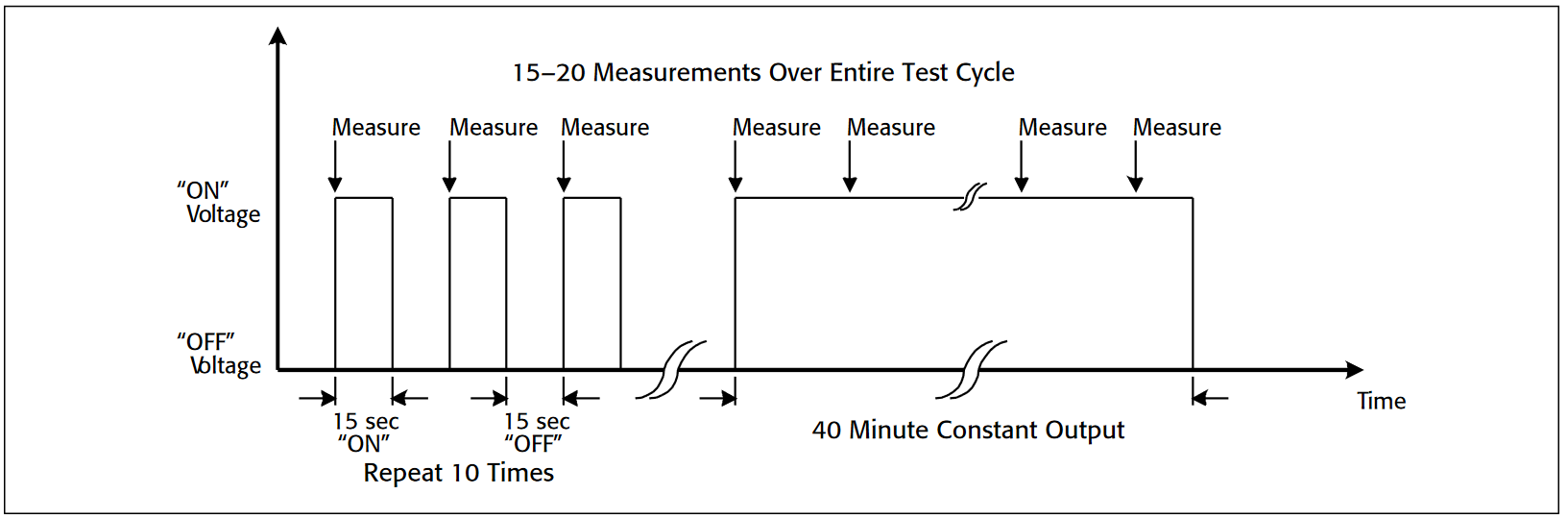
Test System Description
The basic requirement for burn-in testing is to measure the voltage drop across the load resistor placed across the output of each switching power supply (Figure 1) during the entire test cycle. Test cycle duration can range from less than an hour to many days, depending on the quality requirements determined by the manufacturer.
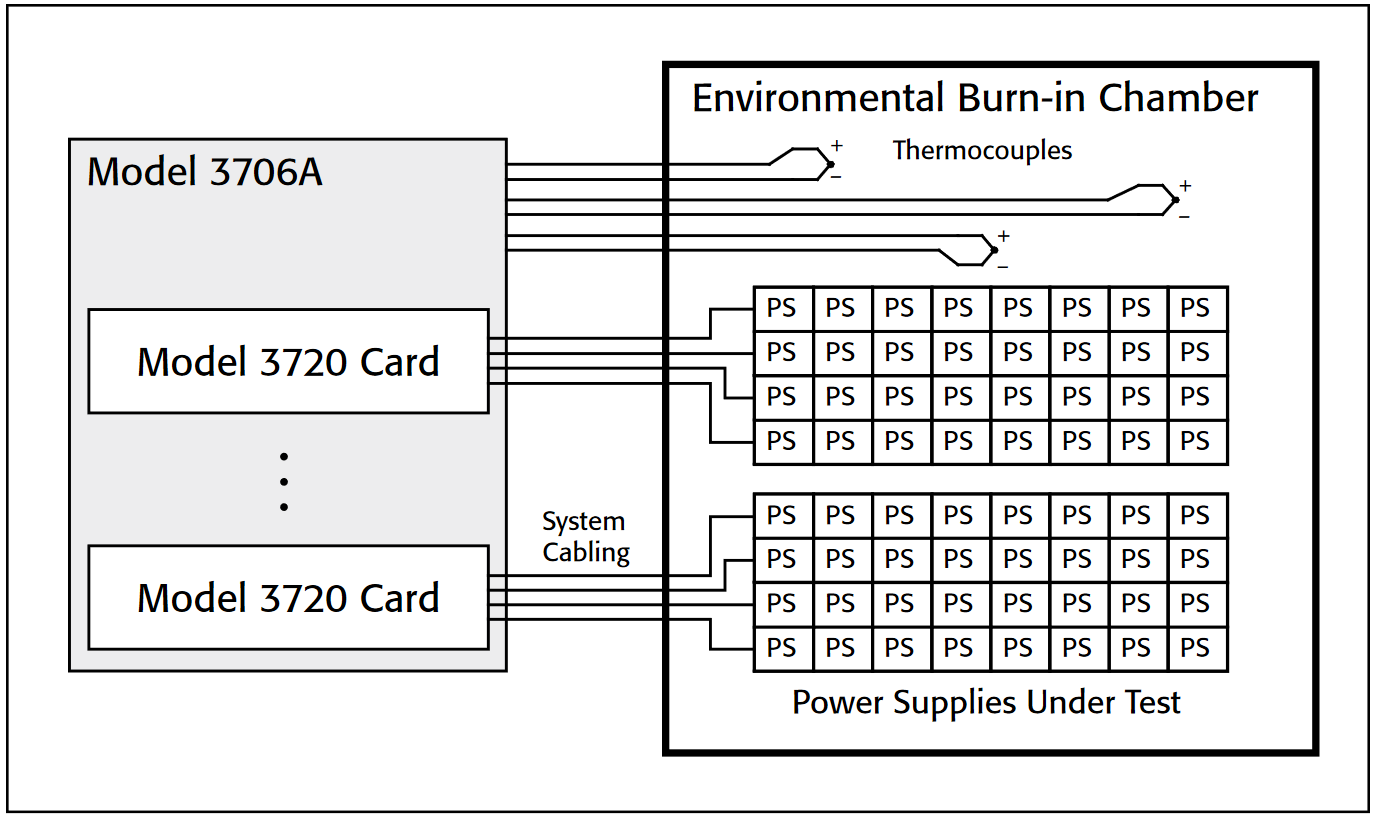
Figure 3 illustrates an example of a 300-channel burn-in system in an environmental chamber, using the Model 3706A 7½-digit DMM to make the required voltage measurement on each power supply. Six Model 3720 Dual 1×30 Multiplexer Cards are used to connect the inputs of the Model 3706A to each power supply. The Model 3720 Multiplexer Card is used in this case because each card can monitor up to 60 channels at 300VDC. Each channel has two connections (HI and LO) for each power supply.
A typical specification for a power supply is to output 5V with 10% accuracy, which presents no measurement problem for a the integrated 7½-digit DMM in the Model 3706A. As shown in Figure 2, when the output is cycled every 15 seconds, the DMM must make measurements on 300 channels during the 15 second “on” time. Setting the integration rate or measurement time to be as fast as possible (NPLC = 0.001) and disabling all filters makes performing these measurements fast and easy.
The Model 3706A/3720 Multimeter/Data Acquisition System can be used to verify the temperature profile of the environmental temperature chamber independently. By plugging one Model 3720 60-channel differential multiplexer module into the Model 3706A, the system can accommodate up to 60 thermocouples.
Typical Sources of Error
Environmental Noise
Placing hundreds of switching power supplies into an environmental temperature chamber makes it extremely difficult to make accurate voltage measurements because switching power supplies radiate high frequency noise. If the ground connection is noisy, traditional data acquisition systems will be unable to make satisfactory measurements. The system described here requires scanning across multiple channels rapidly with the high impedance input of the DMM. In this situation, it can be difficult to distinguish between 5V and 0V on adjacent channels. Even with the Model 3706A’s superior CMRR, NMRR and 26-bit ADC, making the distinction can be difficult. However, Keithley has developed an algorithm (described elsewhere in this application note) that simplifies this problem.
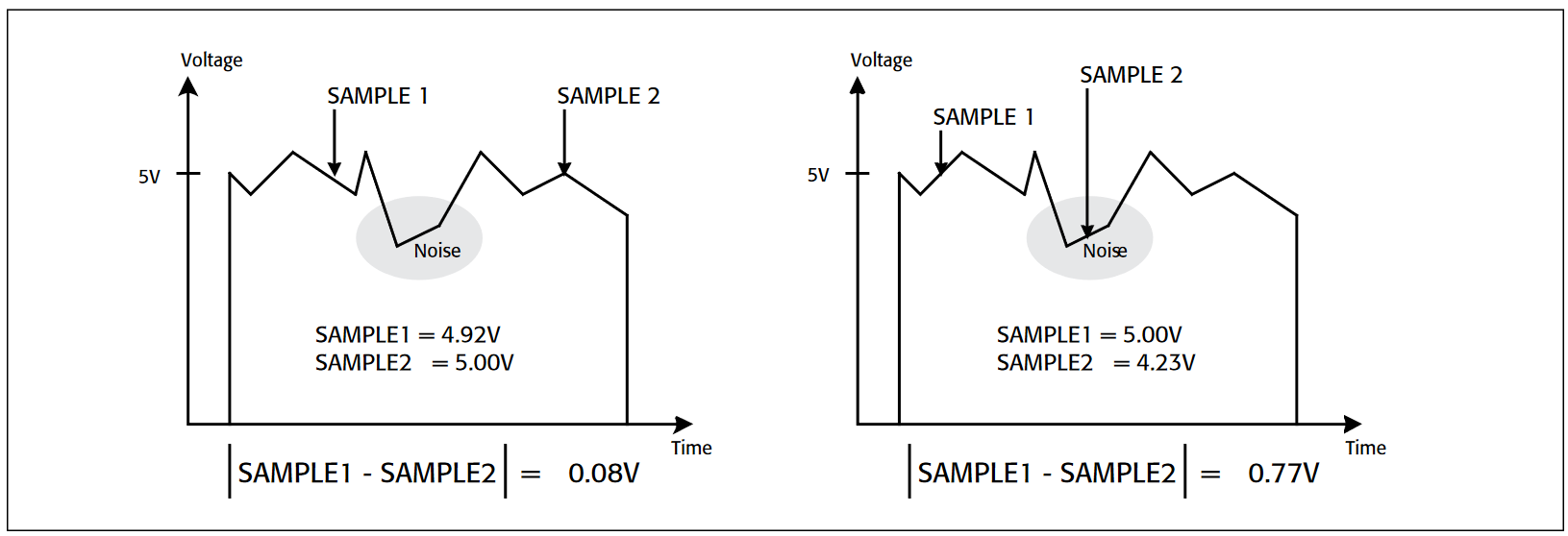
To determine whether a power supply is good or bad, the test system must not only look at the absolute voltage value, but also at how subsequent readings compare. Figures 4a and 4b show two different results when sampling a noisy signal. Assuming the power supply being tested is known to be acceptable, the figures show how noise can affect the final outcome of the test. Sample 2 in Figure 4b was taken when a noise spike was introduced into the system. This illustrates the importance of taking many samples into account from each power supply or increasing the measurement integration rate.
When measuring 5V on one channel and 0V on the next with very fast scan speed, a DMM may not measure 0V for the second channel. Actually, the first reading may be 4.7V and subsequent readings will decrease to 4.3V, 3.7V and gradually down to 0V. This gradual decrease id due to the RC time constant created by the large DMM input impedance and the capacitance in the test system cabling and fixtures. In contrast, if the measured 5V (i.e. power supply is good) twice, the two results will be similar (generally less than 10mV difference). Therefore, Sample 1 – Sample 2 = Delta, and if Delta is less than 10mV and both samples are within in limits the power supply is accepted. Without using this algorithm, setting a higher measurement integration rate will significantly improve the instrument’s measurement performance in noisy environments, but the resulting scan rate would not be sufficient for the number of channels and time constraints of this application.
Relay Life
Generally, as the power supplies are being tested, their outputs are turned on. Therefore, as the switch mainframe is scanning across each device, the relays are being opened and closed with voltage across their contacts. Actuating a relay in this manner raises the possibility of arcing, which can severely degrade relay life. The relays on the Model 3720 are rated for 108 closures when voltage is not being switched or for 105 closures if a 1A, 300V signal is being continually switched. As the signal levels decrease, the expected life of the relay will increase, so it is important to note the voltage and current levels of each power supply that is to be monitored.
Equipment List
The following equipment is required to assemble the 300-channel switching power supply burn-in test system shown in Figure 3.
- Model 3706A System Switch/Multimeter.
- Six Model 3720 Multiplexer Cards.
- Ten Model 3720-MTC-3 Cables.
- one Model 3720-ST Screw Terminal.
Alternative Solutions
The Model 2700 Multimeter/Data Acquisition System supports up to 80 channels is a nice fit for smaller and more modular systems. The Model 2700 is optimized for smaller HASS systems, or for smaller production lots of power supplies. The 2700 series of switch cards many solutions for temperature monitoring and analog signal routing up to 300V. Output cycling of the power supplies is accomplished using Keithley’s line of PIO digital I/O boards and solid-state relay (SSR) modules.
Test System Safety
Many electrical test systems or instruments are capable of measuring or sourcing hazardous voltage and power levels. It is also possible, under single fault conditions (e.g., a programming error or an instrument failure), to output hazardous levels even when the system indicates no hazard is present.
These high voltage and power levels make it essential to protect operators from any of these hazards at all times. Protection methods include:
- Design test fixtures to prevent operator contact with any hazardous circuit.
- Make sure the device under test is fully enclosed to protect the operator from any flying debris. For example, capacitors and semiconductor devices can explode if too much voltage or power is applied.
- Double insulate all electrical connections that an operator could touch. Double insulation ensures the operator is still protected, even if one insulation layer fails.
- Use high-reliability, fail-safe interlock switches to disconnect power sources when a test fixture cover is opened.
- Where possible, use automated handlers so operators do not require access to the inside of the test fixture or have a need to open guards.
- Provide proper training to all users of the system so they understand all potential hazards and know how to protect themselves from injury.
It is the responsibility of the test system designers, integrators, and installers to make sure operator and maintenance personnel protection is in place and effective.
Find more valuable resources at TEK.COM
Copyright © Tektronix. All rights reserved. Tektronix products are covered by U.S. and foreign patents, issued and pending. Information in this publication supersedes that in all previously published material. Specification and price change privileges reserved. TEKTRONIX and TEK are registered trademarks of Tektronix, Inc. All other trade names referenced are the service marks, trademarks or registered trademarks of their respective companies.
No.2260 Rev.3.24.14