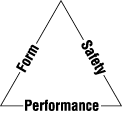
Introduction
Electro-mechanical and automotive systems testing, rotating machinery evaluation, and acoustical behavior analysis are all demanding applications for today's electronic measurement systems. Many mechanical measurements are made at the output of transducers, where microvolt level response signals can be shrouded by transducer generated noise. Often, long duration events, such as vibration tests, will require from minutes to hours of data gathering.
Measuring the tiny oscillations of a mechanical system subject to sudden stimulus or shock requires extremely large oscilloscope dynamic range and high vertical resolution. Product quality and certification testing requires repeatability and accuracy in critical measurements. Precise synchronization with external events, such as the rotation cycle of an engine or motor, makes data easier to record and interpret. Measuring frequency-based components of a time waveform is often needed for solving complex problems such as undesirable vibration.
Finally, documenting product quality profiles is a critical final step in mechanical testing. Engineers and technicians in mechanical fields need to store waveform data and test results in formats that can be easily retrieved for documentation and report generation.
This application note describes techniques of using some of the features and the versatility of a modern digitizing storage oscilloscope - the Tektronix TDS 400A Personal Lab Scope - to make mechanical measurements which have, traditionally, been made by purely mechanical or mechanical-electrical means. It will examine the benefits of using a high CMRR (common mode rejection ratio) differential amplifier for making measurements in the presence of significant common mode noise and DC potentials. It will explain the importance of calibrating the scope to correspond with transducer outputs. And it will conclude with a practical four-step procedure for balancing rotating machinery.
The Personal Lab Scope
The TDS 400A Personal Lab Scope provides a complete test and measurement solution for engineers and technicians in mechanical fields. A precision front end provides 1.5% accuracy, 1 mV/div sensitivity, and a 100 MS/s sample rate on each channel to ensure superior signal fidelity and deliver high acquisition confidence, even for fast transient events. A unique, Tektronix-proprietary, Hi-ResTM acquisition mode provides real time digital filtering to reduce sources of measurement error - particularly noise produced by the wide variety of transducers found in mechanical applications. The Hi-Res Mode1 delivers up to 12 bits of vertical resolution, effectively increasing the scope's dynamic range and allowing users to clearly distinguish even single-shot signals buried in noise.
1For more information about the Hi-Res mode, please contact your local Tektronix sales representative and ask for "Increase Vertical Resolution Using the TDS Hi-Res Mode." - Tek Publication #3GW-8222-2
To eliminate common-mode noise, the TDS 400A equipped with the Tektronix ADA400A Differential Amplifier, provides a common-mode rejection ratio (CMRR) of 100,000:1 - allowing users to view the tiny, microvolt level oscillations of mechanical signals in the presence of high-amplitude noise. This capability, when combined with the TDS 400A's Hi-Res mode, is especially useful for viewing mechanical events, such as bearing noise, that are not strictly repetitive but are constantly changing.
The TDS 400A Personal Lab Scope provides simple operation with an intuitive graphical user interface that makes test setup, waveform capture and display very easy, even for the novice user. Two to four channel operation allows simultaneous acquisition and display of multiple waveforms. 120K record lengths on all channels gives engineers and technicians the ability to capture and analyze slowly-varying events and view cause-and-effect relationships.
A Roll Mode Display provides dynamic event monitoring, allowing users to observe slow changes as they happen instead of waiting until the entire acquisition is complete. The Roll Mode provides a familiar-looking display for those who have used chart recorders in the past, while eliminating the mechanical inertia, slow response, and break-down problems of mechanical recording equipment.
For signal processing and analysis, the Personal Lab Scope provides 25 automatic measurements of frequency required critical waveform parameters in terms familiar to engineers and technicians. A real-time FFT (Fast Fourier Transform) function allows mechanical engineers to examine the frequency (harmonic) components of waveforms in vibration and resonance tests, and reveal the true source of design problems. A Template Test mode provides the means to conduct on-board pass/fail tests against reference or "golden" waveforms. And 120K record length reference waveforms can be sorted for comparison with captured signals. These features not only ensure that the user obtains "total information" from the acquired waveform, but also saves time by dramatically reducing the need for offline analysis with external computers.
Finally, the Personal Lab Scope provides the data storage and retrieval features engineers and technicians needed to produce product quality profiles, vibration analysis reports, results from shock impact test, and other test results. Waveform data and test results can be downloaded to the scope's 3.5 inch DOS floppy drive in fourteen different industry-standard waveform formats. Data can be imported into spreadsheet and MathCad® formats for use in report-generation programs such as EXCEL®, Lotus 1-2-3®, and QuatroPro®. Waveforms and measurement results can also be saved in popular desktop publishing formats - PCX, TIFF, BITMAP, MS Word -0 for use in Windows and Macintosh wordprocessing programs. Or, with the TDS 400A Printer Pack option, users can generate hardcopies of any screen display.
Differential Mechanical Measurements
Electromechanical transducers transform physical or mechanical actions into their electrical equivalents. These electrical signals can then be viewed as voltage waveforms on an oscilloscope screen. Today's electromechanical transducers can convert almost any physical quantity - force, displacement, pressure, temperature, etc. - into its electrical equivalent.
Unfortunately, transducer outputs are inherently low level, and the signal is often routed through hostile environments that introduce power line and RF interferences. The ADA400A Differential Amplifier has three characteristics that make it especially useful for making mechanical measurements in such environments: high sensitivity (in the microvolt range), the ability to reject unwanted common signals and noise (high common mode rejection ratio - CMRR), and the ability to distinguish small signals riding on above-ground DC potentials. It also incorporates high and low frequency roll-off filters which enable selective attenuation or elimination of undesirable signals - such as power line hum, base line float, and high frequency noise.
NOTE: In the United States, OSHA (Occupational Health and Safety Act) requires that all test equipment be connected to the power line via a 3-wire power cord with the third wire grounded (unless line equipment is double-insulated). Therefore it is not permissible to "float" an instrument to obtain signal isolation. The differential amplifier lets you look at small signals that are elevated from ground while preserving the instrument safety ground connections. (See instrument specifications for maximum input levels.)
Signal-Ended Amplifiers
The easiest transducers to use with oscilloscopes are the self-generating types. Many have BNC connectors that simplify connection to a coax cable or to special low-noise coax.
Passive transducers, such as strain gauges, require external excitation and some means of completing the bridge configuration shown in Figure 1. Differential amplifiers are usually necessary when using passive transducers such as the strain gauge, because the gauge bridge and associated power supply present an elevated output signal to the oscilloscope.
Figure 1.
Not all mechanical transducer outputs, however, need the special capabilities of the differential amplifier. For instance, the vibration transducers used in the balancing application given later have a "displacement" output of 10 mV/mil, with a 5% accuracy. Typical balancing operations will produce outputs in the range of 5 mV to over 100 mV peak-to-peak. Here the 1 mV/div sensitivity of the TDS 400A is suitable for this type of application.
The Importance of Calibration
Readouts in "volts" and "time" are suitable for some applications, but users in the mechanical sciences are more often interested in such parameters as rotational speed in RPMs, pressure in PSI, acceleration in Gs, and displacement in inches or centimeters. Care should be taken, therefore, to calibrate the oscilloscope so that its display accurately corresponds to familiar parameters.
There are two basic approaches to calibrating a scope for a specific transducer output: (1) using calibration data supplied by the manufacturer; and (2) applying a known mechanical quantity to the transducer and adjusting the scope display to read out in a corresponding number of divisions.
Calibration Data Supplied by the Manufacturer. Commercial transducer manufacturers supply conversion data and/or graphs that relate the physical parameter to its electrical equivalent.
For example, self-generating pressure transducers are usually specified in terms of millivolts/PSI. Piezoelectric transducers of all types are usually expressed in both millivolts/measurand and picocoulombs/mesurand. Commercial strain gauge transducers are usually specified in millivolt/volt of the full scale measurand. (The volt refers to the associated bridge voltage and is one of the factors governing sensitivity.)
Calibration by Known Mechanical Quantities. Perhaps the simplest way of obtaining or verifying system calibration is to apply an appropriate known quantity to either the transducer itself, or to the instrumented structure.
For example, accurate calibration of hydraulic pressure can be made by connecting the pressure transducer to a deadweight tester, selecting the desired full-scale PSI in equivalent dead-weight and adjusting the oscilloscope sensitivity to give some convenient full-scale reading - such as 10 PSI/div. The TDS 400A's vertical-bar measurement cursors make such calibrations extremely easy, as we`ll see in the following application.
Using the Personal Lab Scope to Balance Rotating Machinery
Vibration is perhaps the most common manifestation of mechanical imperfection. In general, rotating machinery, such as air distribution fans and blowers, will be the source of everyday vibration.
The techniques for measuring and correcting imbalance in rotating machinery can vary from simple trial-and-error methods, to using sophisticated computer-aided techniques.
This application demonstrates how the TDS 400A Personal Lab Scope can be used with three readily available transducers to perform static and dynamic balancing of rotating devices. A significant advantage of the TDS 400A is its portability and ease of use when performing "on-site" balancing operations on large fan or blower installations, with consequent savings in labor and transportation costs.
![]() |
Figure 2. |
![]() |
Figure 3. |
Understanding Static and Dynamic Balance. A rotor is statically balanced when the axis of rotation (the bearing axis) passes through the rotor's center of gravity (Figure 2). In this condition, a rotor supported on frictionless bearings exhibits no tendency to seek a particular angular position in response to gravitational forces. The rotor will not be dynamically balanced, however, unless the bearing axis also coincides with the principal inertial axis (Figure 3). Static imbalance results in a FREE FORCE. Dynamic imbalance results in a FREE COUPLE.
Factors Affecting Measured Phase Shift. Structural and bearing resonances and seismic type transducers used near their resonant frequency can affect the measured phase shift. Furthermore, the measured phase of imbalance changes through 180 degrees as the rotating member goes through its structural resonance frequency. For this reason it is desirable to operate the rotating device either well below or well above structural and bearing resonances.
Balance Plane Interaction. When the bearings and balance planes are widely separated, there will be considerable balance plane interaction because balance weights added to one plane will affect both the left and right bearings. However, when the bearings and balance planes are close together, there will be little balance plane interaction. In this case, the one balance plane and bearing located close to each other are all that is needed to perform an adequate balance job.
Transducer Installation. Transducers should be mounted in a horizontal plane on or close to the bearing housings - one on each of two housings. There are two reasons for this placement:
- The mounts are usually much more "flexible" in the horizontal plane than the vertical, so horizontal placement will result in a greater transducer output.
- Conventional balancing machines employ bearing "saddles" which are flexible in the horizontal plane, so it's easy to attach horizontal transducers right on the saddles for maximum output.
Transducers can be attached to bearing mounts with C-clamps, magnets, or, in some cases, double adhesive tape.
![]() |
Figure 4. |
Magnetic Pickup (Pip Coil). The purpose of the pip coil is to obtain information on shaft position. The coil produces an output proportional to the velocity of any ferrous projection, or discontinuity, passing the sensor head. This discontinuity can be a set screw, bolt, key, keyway, drilled hole, or a very small steel bar taped to the shaft. The position of the discontinuity becomes the 0 degree reference for the balancing operations that follow.
The pip coil should be mounted in the same plane and on the same side as the displacement transducers; and close to, but not touching, the discontinuity (Figure 4). For on-site, temporary mounting, the pip coil can be mounted on the machinist magnetic-base tool support.
Note: Modern transducers, such as optical transducers, can also be used to indicate rotational position. In addition, the external clock on the TDS 400A can be used to acquire signals in sync with the rotational angle of the rotor. Each angular degree of rotation can correspond to one external clock. Using this technique, the acquired data is always displayed with respect to clock cycles, which correspond to the rotor's angular position.*
*For more information on the TDS 400A's External Clock, please contact your local Tektronix sales representative and ask for Tektronix Publication #3GW-10380-0.
Practical Balancing
Instrument Set-up. Connect the left and right vibration transducer "displacement" outputs to channel 1 and channel 2 of the TDS 400A. Select these channels for display by pressing the CH1 and CH2 buttons on the front panel. Initially set the vertical scaling for 50 mV/div (Figure 5).
Figure 5.
Connect the pip coil to channel 3 of the scope and display its output signal by pressing CH3 on the front panel. Adjust the vertical scale for this signal to 0.2 V/div.
The TDS 400A allows the user to trigger one or more channels off one of the other channels. In this case, both channels 1 and 2 can be triggered from the pip coil signal on channel 3. To do this, select TRIGGER from the Main Menu displayed on the screen; then select CH3 as the trigger SOURCE. The pip coil signal on CH3 is now the trigger signal; and the time between two successive triggers is equivalent to one complete shaft rotation (360 degrees).
Prebalancing Steps, Determining Resonance Frequencies. There are two ways to determine the first structural resonance frequency (first critical) with the transducers in place:
- Increase the speed from rest until the measured displacement shows a marked increase in amplitude. At resonance the amplitude of the two transducer signals will be at maximum and will have shifted phase by 90 degrees compared with the rotational marker.
- Because many rotating devices run at a fixed speed, it may not be possible to use method 1. A convenient way to determine resonance is to bump- or push-release the bearings, and store the damped waveform (Figure 6).
Figure 6.
Use the TDS 400A's vertical bar cursors to measure the time between two peaks on the damped waveform. This will give the exact first resonance.
RPM:
= 60 / time in seconds
= 60 / 22 x 10-3 seconds
= 2700 RPM
Alternately, the TDS 400A's FFT capability (not shown) can be used to measure the first resonance frequency directly, in the frequency domain. To access the TDS 400A's FFT capability, press the MORE button in the main menu. Then select FFT MATH (Single Waveform Math) for the signal whose first resonance frequency is to be measured. By simply placing the TDS 400A's measurement cursor on the second peak shown on the screen, the user can obtain a direct readout of the first resonant frequency.
Balancing should be carried out at speeds either substantially below or above the first resonance to avoid phase shift errors. Furthermore, if a device such as a fan or blower normally runs at or near resonance, its speed should be permanently decreased or increased by changing pully diameters, etc., to get away from this undesirable operating area. This step alone should result in a considerable reduction in vibration at the new running speed. If, during the first measurement, vibrations are strong, store the waveforms in the oscilloscope, turn off the device being measured, and make calculations from the stored waveforms.
Caution. Vibration amplitudes can be destructive at resonance if the rotating mass is appreciably out of balance. (See vibration severity guide at the end of this note.)
Balancing Steps. Assuming operating (or test) speed is well below the first structural resonance (first critical):
1. Final Speed in RPM. Measure the time between rotational markers on the pip coil signal using the vertical bar cursors or the automatic PERIOD measurement. Figure 7 shows the time between two adjacent peaks on the displayed waveforms as 33.3 ms.
RPM:
= 60 / time in seconds
= 60 + 33.3 x 10-3 seconds
= 1800 RPM
Figure 7.
2. Find Peak-to-Peak Displacement (mils) and Angular Position for the Trial Weight.
- While holding rotational speed constant, increase the sweep rate one step so that the second rotational marker appears on the screen. Using the TDS 400A's vertical cursors, or its automatic "period" measurement, measure the time between the first and second rotational markers as shown in Figure 8. In this case, we see that the measured period is 33 ms.
Now, 33 ms = 360 degrees
Therefore 1 ms = 10.8 degrees
Note this measurement, as it will be used in calculations that follow. Also, note that the magnetic pick up reference is 0 degree and corresponds with the first vertical graticule mark (at the extreme left edge of the screen).
- Selecting channel 1 and then 2 in turn, adjust the VOLTS/DIV control knob until each transducer waveform is usable. Try to keep the sensitivities the same. Then store the display by pressing RUN/STOP, then SAVE/RECALL on the front panel. A menu will appear that provides a number of alternatives for waveform storage, including: storing as a reference waveform storing to 3.5 inch floppy disk, or storing to external computer memory via GPIB. Here, the waveforms are saved as R1 and R2 reference memory waveforms.
Figure 8 shows the left and right plane outputs at 50 mV/div. The transducer sensitivity is 120 mV/mil, therefore, the displayed sensitivity is 5 mils/div. Therefore, the left plane displacement is 12.5 mils, and the right is 5 mils.
- Next, determine the left plane and right plane angles In this case, the rotor is running well below its first resonance frequency, so measurements are taken from the 0 degree reference marker to the first negative peaks. (If the rotor were running above resonance, the measurement would be taken to the first positive peaks.) Figure 8 shows 30 degrees for the left plane and 40 degrees for the right.
As calculated earlier,
1 ms = 10.8 degree
2.7 ms = 2.7 x 1.8 degree
3.7 ms = 3.7 x 10.8 degree
therefore,
2.7 ms approx. 30 degrees for left plane
3.7 ms approx. 40 degrees for right plane
Figure 8.
3. Applying a Trial Weight. Attach a trial weight to a convenient radius in the plane with the greatest displacement. For example, since the left plane has a displacement of 12.5 mils and a negative peak at 30 degrees, attach a trial weight 30 degrees counter rotation from the magnetic pickup reference in the left plane. The trial weights should be pre-weighted and sized according to the size, speed and imbalance of the device. Trial weights and succeeding permanent weights (or corresponding metal removal) should be placed on the same radius. If this is not practical, weights should be proportional in equivalent ounce inches or gram centimeters from the rotational axis.
4. Second Run with Trial Weight. Bring the rotor up to the previous test speed while observing the second rotational marker. Correct speed is reached when the time between the first and second markers is 33 ms (Figure 9). Verify this speed with the vertical measurement cursors.
Figure 9.
If necessary, change the left and right plane calibrated sensitivities to provide usable displays. Store the display, then measure the new peak-to-peak displacements and phase angles as in step 2.
In this example, Figure 9 shows that a trial weight of 1.08 grams has reduced the left plane displacement from 12.5 mils to 7.3 mils at a phase angle of 40 degrees. The right plane displacement has also been reduced from 5 mils to 3 mils at a phase angle of 40 degrees.
Finding the Correct Weight. The correct weight can be computed from the following equation.
Remove the trial weight and add the new calculated weight of 2.6 grams 40 degrees counter rotation from the 0 degree reference in the left plane.
Figure 10 shows the results of this simple four-step process.
Figure 10.
Vibration is down to approximately 0.6 mils. Left plane displacement is down from the original 5 mils to approx 0.6 mils without applying weight to that plane. This is because the original right plane vibration was caused by imbalance in the left plane. This effect is called balance plane interaction.
When balance plane interaction makes it difficult to reduce vibration to acceptable levels, additional steps are required before balance is achieved, but the principles remain the same.
Summary
This application note has demonstrated how easy it is to use the TDS 400A Personal Lab Scope to balance rotating equipment. Its on-board measurement set and easy-to-read display allows the user to quickly determine rotor speed, critical resonance frequencies, peak-to-peak displacement of the rotor, and the angular position for a trial weight to correct imbalances.
The TDS 400A Personal Lab Scope, coupled with the ADA400A Differential Amplifier, delivers a complete test and measurement solution for mechanical measurements all the way from signal conditioning to acquisition confidence, waveform analysis, and sophisticated results generation.
Mechanical Application Areas for the Personal Lab Scope
As with most disciplines, applications are many and varied, and are being added to as new uses are found for the "complete solution" offered by the TDS 400A Personal Lab Scope. Here are a few examples:
Environmental Labs - Shock and impact testing. Destructive and nondestructive testing. Life testing.
Engineering - X-Y displays of force versus displacement, or torque versus rotation. FFT analysis for vibration and resonance studies. External event synchronization with the scope's external clock input. Dynamic event monitoring using Roll Mode. Template pass/fail testing.
Building Maintenance - Preventive maintenance on fans, motors, bearings, etc. By storing "normal" condition waveforms for parameters such as bearing noise, vibration, and rotation speed, they can be used as reference waveforms during periodic checks. Differential amplifiers, such as the ADA400A, extend the useful range of vibration transducers, and allow the use4r to view tiny vibration levels in sites that are to be used for delicate equipment - laser trimmers, optical measuring devices, etc.
Production - Monitoring performance of heavy equipment, such as diecasting presses, injection molding, and hydraulic machinery to insure uniform quality of finished product.
Electronic Troubleshooting - General electronic equipment troubleshooting and repair in the lab or on the production floor.
General - Many applications are simple "on/off" situations designed to resolve specific problems. The configurability of the Personal Lab Scope provides from one to four channels of information at 1 mV/div sensitivity. When used with the ADA400A Differential Amplifier, differential measurements can be made to 10 µV/div.