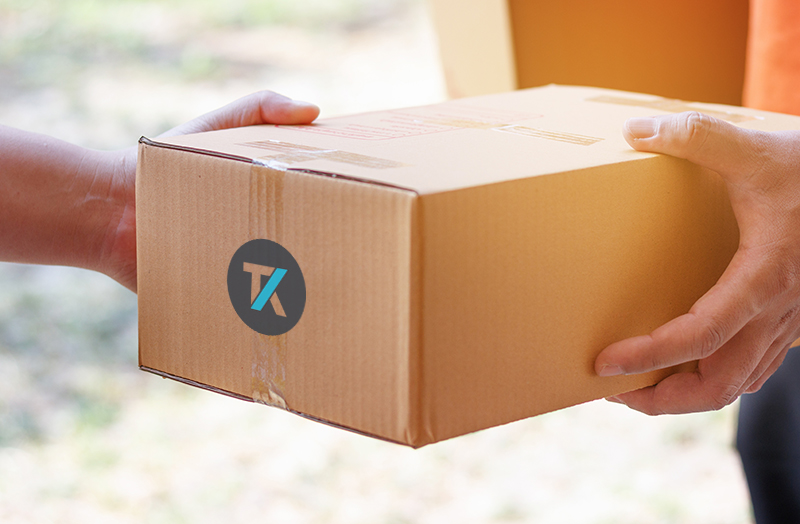
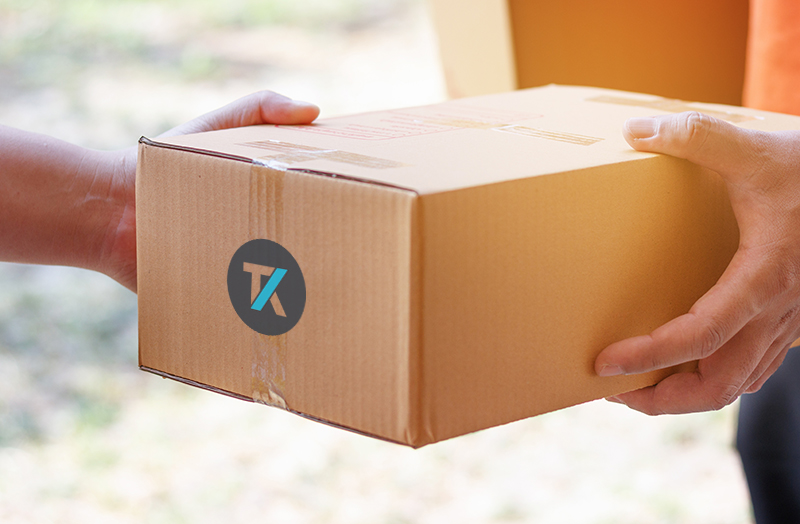
Making sure that your workforce has the equipment and tools they need to get their job done can be fraught with difficulty (and headaches)! If this responsibility falls to you then I’m sure you are aware of the challenges it presents. Just ask yourself these four questions:
- Does your team send in equipment according to required service intervals?
- Do your calibration and maintenance programs distract your workforce?
- How long does it take to get your equipment serviced?
- Do you suffer from downtime while your equipment is being serviced?
Chances are you’ve heard these questions before, and you know that the answers have a bearing on risk and compliance with any number of industry standards and requirements.
One example where risk and compliance are paramount is with automotive services. If you’re in this industry, you understand it is critical to follow proper guidelines on torque during mechanical work such as wheel installations, engine or transmission repair, or even installing oil drain plugs. Relying on your technicians’ best guesses on correct torque (especially if they are less experienced) can expose you to significant liability. Properly calibrated torque wrenches can reduce that liability and increase your customers’ confidence in the quality of your services.
But how do you know if the torque wrenches in your shop are still in calibration? The more frequently the wrenches are used, the more frequently calibration is needed. Simply sending torque wrenches in for calibration once a year, especially if you have a busy shop, may not provide the assurance of compliance your business and customers rely on.
You need a solution that ensures your technicians have calibrated torque wrenches when they are needed – and that your technicians don’t inadvertently use a torque wrench that’s past its equipment calibration due date. Otherwise, you could be facing a situation where every vehicle that torque wrench touched is a potential liability.
We take torque wrench calibration seriously! Our automated high-volume, high-precision torque calibration stations have a measurement accuracy of 0.25% and our laboratories are accredited to the highest level of compliance with industry standards such as ISO 9001:2015 and ISO/IEC 17025: 2017. And our torque testing processes are some of the most rigorous in the industry.
By investing in automated, state-of-the-art calibration test equipment, we can reduce opportunities for human measurement error, while increasing our ability to rapid calibrate your torque wrenches to the latest standards.
The Active Exchange Program Meets Your Unique Needs
Active Exchange eliminates the need to track down equipment and maintain service records, while enabling you to achieve 100% equipment uptime.
- Focus on your job, not servicing your equipment.
- Advanced replacement of your workforce’s tools
- Maximize uptime
- Equipment is stored and maintained by Tektronix
- One service provider to manage all calibration and maintenance needs
- Worry-free logistics
- 24/7 visibility of your assets in CalWeb – our cloud-based asset management solution
- Scalability at an affordable price
- Onsite options available
Get started with a business evaluation and risk analysis, where we dive in and begin to understand your compliance needs and challenges. We’ll then propose a detailed solution to address your requirements and develop a schedule and milestones to deliver it.
To learn more about the Active Exchange program, visit our website.