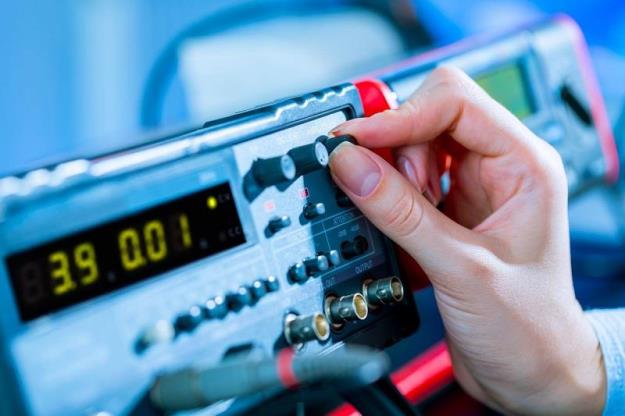
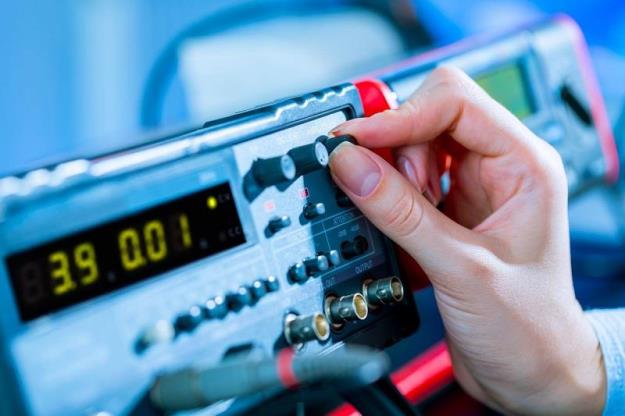
Not all test and measurement equipment calibrations are created equally. There are several factors to consider when selecting a service provider to ensure you receive a quality calibration. In simple terms, Equipment calibration is the comparison of a measurement device (an unknown) against an equal or better standard, and often requires certification and documentation.
In mission-critical industries, such as aerospace, defense, semiconductor, automotive, wireless, and others, test and measurement equipment calibrations are required for passing industry audits. Smooth your process for passing an audit by ensuring you receive quality calibrations on your test and measurement equipment. Additionally, in these industries, incorrect and unreliable calibration can jeopardize product reliability and your company’s reputation. Below are five considerations that will help verify that you are receiving a top-quality calibration.
- Understand the critical driver for calibration.
Calibrations are part of the engineering process and required to validate your measurements over a period of time. When considering calibration as a technical function, it needs to fit the due diligence that you apply towards your testing and your product. Why is that important? One word… risk.
Proper calibration reduces your risk of failing audit as well as product rework, recalls, returns, and repairs. With the right calibration, you can be more efficient with your time to market and testing while minimizing your risk, which reduces your total cost of test.
- Understand your company’s calibration requirements.
Does your business operate in a regulated environment? Has your company defined specific quality requirements to ensure risk is being mitigated? Ask yourself, how certain do I need to be in my measurements? Do all my instruments need to be calibrated? Does my quality policy require certification and/or accredited calibrations, and what are the documentation requirements?
Not all calibrations are created equally. Does your calibration supplier engineer, design, and service test and measurement equipment, understanding it inside and out? Do they offer multiple levels of ANSI/NCSL Z540 and ISO/IEC 17025 accredited calibrations, or do they simply focus on a base level of commercial calibration? For calibration quality success, seek a supplier that truly understands test and measurement technology, such as an OEM of T&M equipment.
- Conduct a detailed analysis of your calibration supplier.
These are some questions you should ask of your calibration supplier.
- Can you calibrate to the full manufacturer’s test procedure?
- Can you provide me with an example calibration certificate/data for instrument model X?
- What percentage of my equipment will you calibrate yourself and how much will you subcontract elsewhere?
- What turnaround time can you supply (typically) for different types of measurement instruments?
- Can you customize a program to fit my needs?
- How will the certificate be delivered and accessed later?
- Understand what you should include in a request for calibration.
Knowing what to include in your request for service, or knowing how to evaluate a service provider’s proposal, is crucial to ensuring a quality calibration. First, select the right level of calibration based on your unique requirements. Do you need standard (Z540.1) or accredited calibration (17025, Z540.3)? Does data need to be included? How will any adjustments be performed? Your quality policy should drive these requirements.
Make sure to request the company’s scope of accreditation to ensure that the provider offers a successful track record of delivering the requested calibration level for your specific type of instrument.
- Understand the importance of accreditation.
It is possible to receive a valid calibration from a laboratory that's not accredited. The difference is that labs that have not been accredited by an independent accrediting body like A2LA or ANAB cannot prove that they are in fact compliant with all parts of your selected calibration standard.
They may follow the proper processes but partnering with an accredited quality calibration service is the only way to ensure your calibration provider is compliant with your required industry standards.
Any calibration company can claim that they comply with international standards, but only an accredited company can prove it.
Calibration is a crucial part of your engineering process. It validates your results from your test and measurement equipment. It reduces the need to recall or rework product because of poor measurements. These five points will help you to ask the necessary questions to ensure you receive the best quality calibration and will ensure that you get what you pay for.
For additional detail on these five points, and other insights into ensuring a quality calibration, be sure to watch the on-demand webinar.