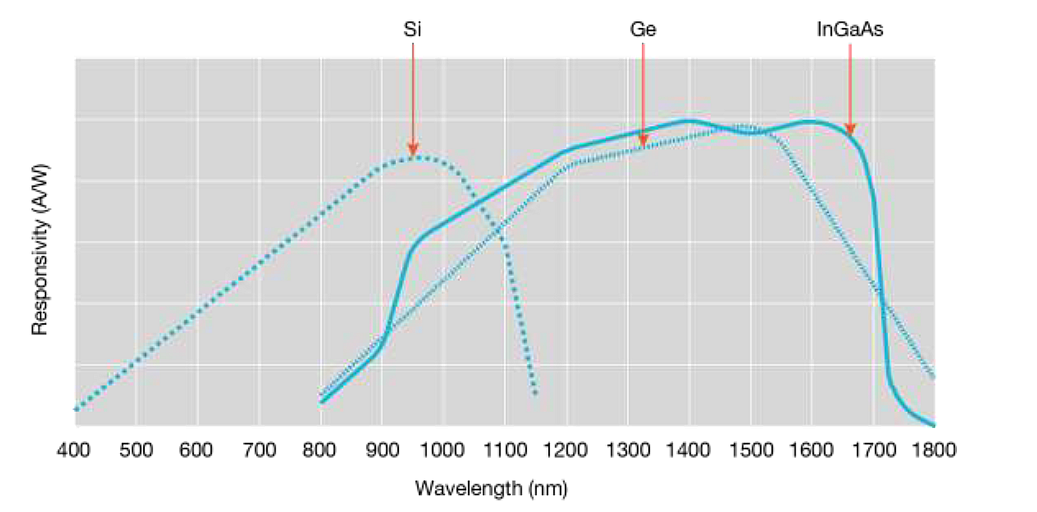
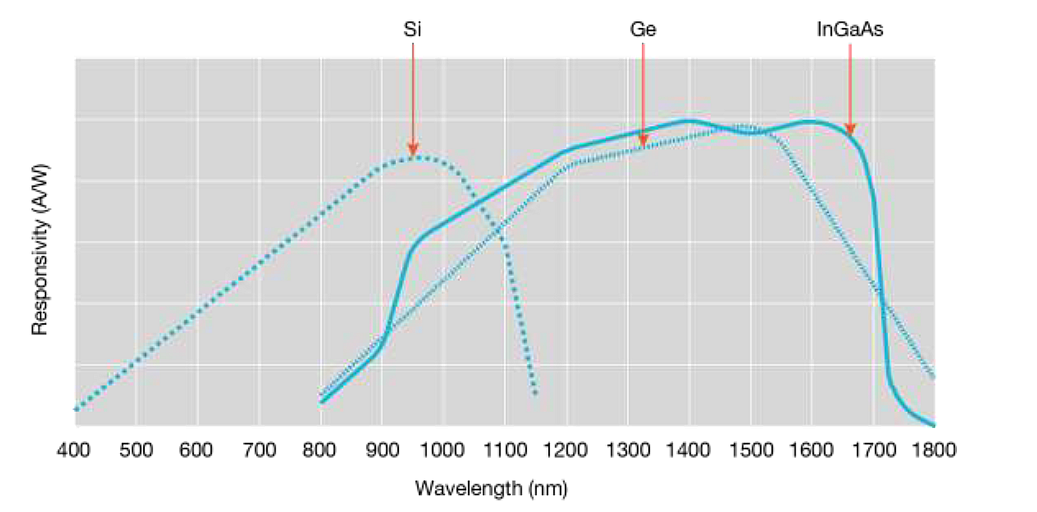
Diode-based optical devices are expected to see considerable market growth in the coming years as 3D sensing technologies go mainstream, as we discussed in this blog post. Regardless of the type of laser diode, eventually its optical power will need to be measured in the production environment – the more accurately the better.
Indeed, accurate measurements are vital to achieving high manufacturing yields --- inconsistent radiation collection or inaccurate measurements can cause good devices to be graded incorrectly or even rejected completely. Or worse, bad devices might pass the screening process and get sent along to end customers.
In a production environment where speed is critical, there are two methods for capturing the optical power of radiant sources using P-I-N (positive-doped layer, intrinsic layer, negative-doped layer) photodetectors. The first method is direct coupling to the photodetector and the second is coupling to the detector through an integrating sphere.
The direct coupling method, where the emitted radiation falls directly on the detector and creates a current, is simple and straightforward. However, it can be challenging to obtain accurate measurements due to a variety of potential problems including underfill and overfill, beam alignment, polarization, over saturation of detectors and back reflection.
For these reasons, the preferred method is to use an integrating sphere and detector connected to an optical power meter or electrometer. An integrating sphere is essentially a spherical cavity with a diffuse reflective interior surface that’s designed to distribute the optical power from a radiant source uniformly over its interior. A detector on the inside of the sphere therefore receives uniform irradiance allowing for consistent and repeatable measurements.
The use of an integrating sphere for optical power measurement eliminates the problems encountered in the direct coupling method, but there are some aspects about using an integrating sphere you should be aware of as you set up your manufacturing lines to deliver maximum yield. Here are four important things to know.
Pay attention to internal reflectance -- For accurate measurements, it is critical for the internal surface of the sphere to be highly reflective at the wavelength of light to be measured. Traditionally, integrating spheres are constructed using two hollow hemispheres. The interior is coated with a material that is reflective at the wavelength of interest and diffuses the input light. Spheres utilizing this type of coating are sensitive to environmental changes (humidity, atmospheric conditions: acids, bases, and vacuum). To maintain a high level of accuracy, it’s advisable to recoat once a year.
Calibrate the sphere and detector together -- The characteristics of a specific sphere and detector are unique to the degree that they must be calibrated as a set. Once calibrated, this detector/sphere pair must remain together to maintain the accuracy of the calibration. Separating the detector from the sphere or changing the angular orientation of the detector by rotating it will change the calibrated response of the sphere/detector pair.
Pick the right detector for your wavelength -- The source wavelength influences the choice of detector material as well as sphere coating. The wavelength responsivity of the detector material (Ge, InGaAs, Si) varies significantly as shown in the chart below. For visible to near-IR measurements (500–1,000 nm), the Si detector is the best choice. Ge detectors work well with sources with wavelengths of 850–1,450 nm. InGaAs detectors respond from 850 nm to 1600 nm, with excellent linearity from 1,400 nm to 1,600 nm.
The wavelength responsivity of detector materials varies considerably.
Electrometers can be used instead of optical power meters -- Optical power meters consist of a low-level ammeter or electrometer combined with special features for photonics research or engineering applications. Keithley Instruments defines an electrometer as a highly refined DC multimeter that’s optimized for low-level current measurements. A Keithley electrometer can be substituted for an optical power meter for use with integrating spheres and is the recommended option.
Keithley test solutions are widely adopted for testing laser diodes. You can learn more about 3D sensing applications here where you will also find more details on using Keithley instruments to perform electrical testing on diode-based devices. If you’re working on projects involving diode-based optical devices and 3D sensing, we look forward to hearing from you about the characterization, validation and other test challenges you’re facing.